AFFRI WIKI 200
Fully automatic and motorized Hardness tester for Vickers and Knoop tests
The Vickers hardness tester AFFRI WIKI 200 is a fully automatic and motorized hardness testing machine with test loads from 0,001 to 100 kgf. It is suitable for CHD (Case Hardness Depth) tests on multiple samples. Wiki 200 JS is conform to ASTM and ISO hardness testing standard.
- Test loads from 1 gf to 100 kgf (0.0098 to 980.7 N)
- Vickers ISO 6507 / ASTM E-384 / ASTM E-92 HV0.001 – HV0.005 – HV0.01 – HV0.015 – HV0.02 – HV0.025 – HV0.05 – HV0.1 – HV0.2 – HV0.3 – HV0.5 – HV1 – HV2 – HV3 – HV5 – HV10 – HV20 – HV30 – HV50 – HV100
- Knoop ISO 4545 / ASTM E-384 / ASTM E-92 HK0.01 – HK0.02 – HK0.025 – HK0.05 – HK0.1 – HK0.2 – HK0.3 – HK0.5 – HK1
- Brinell ISO 6506 / ASTM E-10 HBW 1/1 – HBW 1/1.25 – HBW 1/2.5 – HBW 2.5/62.5 – HBW 1/5 – HBW 1/10 – HBW 1/30 – HBW 2.5/6.25 – HBW 2.5/7.8125 – HBW 2.5/15.625 – HBW 2.5/31.25 – HBW 2.5/62.5
One Touch Measuremet
Simply press the start button, and the head will execute the entire testing cycle automatically and seamlessly, ensuring no step is missed:
- Automatic detection and contact with the sample.
- Precise execution of each predefined pattern and indentation, regardless of the number required.
- Automatic focus adjustment and accurate reading for both single and multi-indentation tests.
Once the process is complete, results are promptly displayed, including the indentation image, detailed statistics, and CHD charts.
What are its applications?
AFFRI WIKI 200 hardness tester is designed for performing micro and macro Vickers hardness tests and CHD case depth evaluations on various metals, such as iron, steel, tempered steel, cast iron, brass, aluminum, copper, and metal alloys. It is also ideal for testing materials treated with heat processes, including hardening, nitriding, cementation, and hardfacing. Additionally, it supports Knoop hardness testing on ceramics and glass.
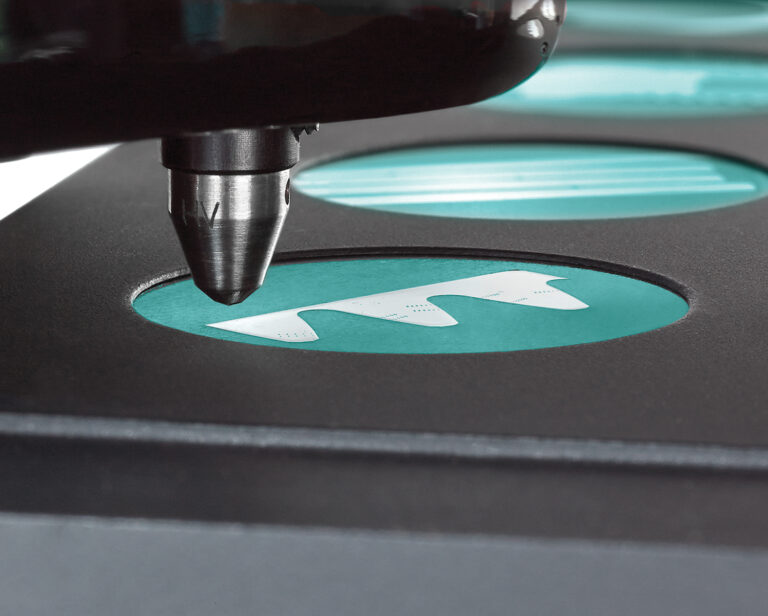
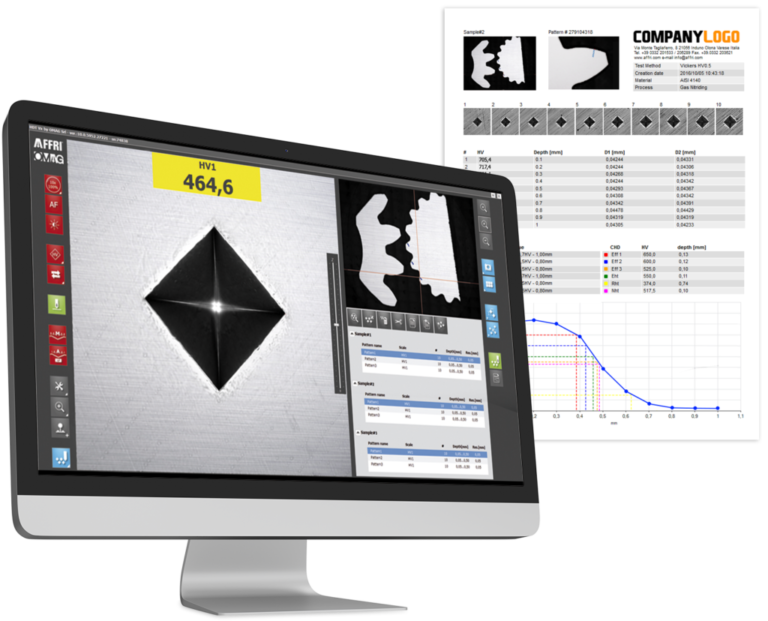
Don’t Waste Your Time
Micro hardness tester AFFRI WIKI 200 has software designed for intuitive and simple use. All you have to do, for case hardness depth, with three easy steps:
- Obtain a perfect, detailed, high-resolution panoramic view of the sample using the panoramic feature. The picture is clear, sharp, and without any distortion.
- Create, save, open, modify, copy or paste Vickers multi-tests to predefined locations with a simple click. Create case depth traverses or fill a surface with indentation points to control sample uniformity.
- The hardness tester brings you to the right position, indents the sample, measures, and generates data dynamically. Review results in graphical and/or tabular format. Export results to any spreadsheet application, or simply print standard or customized reports.
The Vickers hardness tester teaches the operator how to move, saving time and money, thus increasing the accuracy of results.
Software
The AFFRI WIKI 200 software is designed to meet all measurement requirements while remaining accessible to users of all skill levels.
This “SMART SOFTWARE” is highly intuitive yet equipped with all the features necessary for performing basic or advanced Vickers hardness tests, including:
- Easy-to-execute single Vickers tests
- Automatic scale conversion (Rockwell, Brinell, Knoop, ASTM, ISO)
- Multiple-sample and multi-cycle hardness testing with automated operation
- Automated Vickers case hardness depth analysis (CHD, NHT, EHT, RHT, and more)
- Layer thickness measurements
- Crack detection and assessment
- Automated Vickers testing for weld joints
- Direct export of results via Ethernet
- Fully customizable test reports, including client logos, sample details, indentation images, statistical data, and graphical representations
This software offers a comprehensive and efficient solution for a variety of testing applications, ensuring precision and convenience.
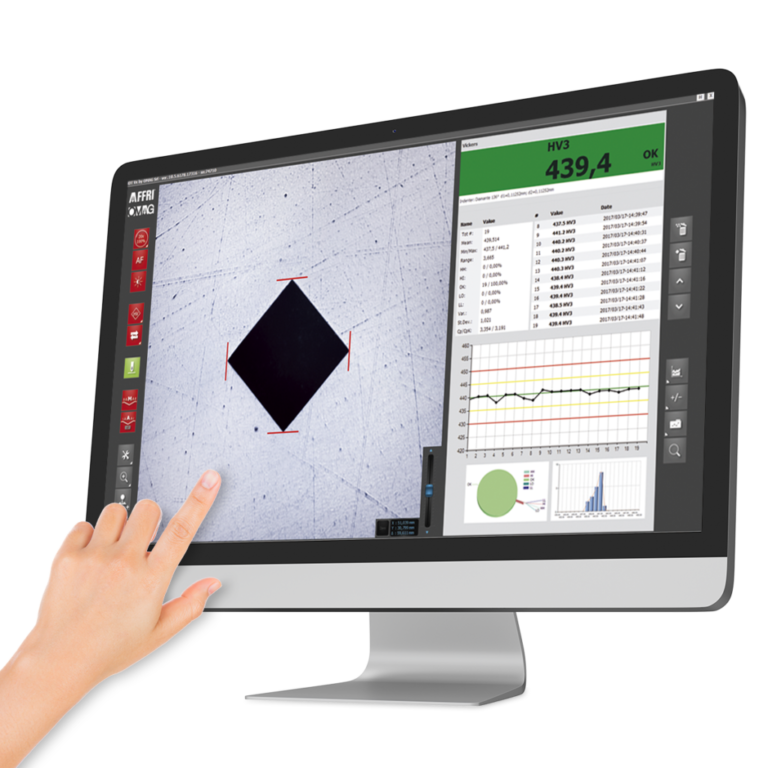
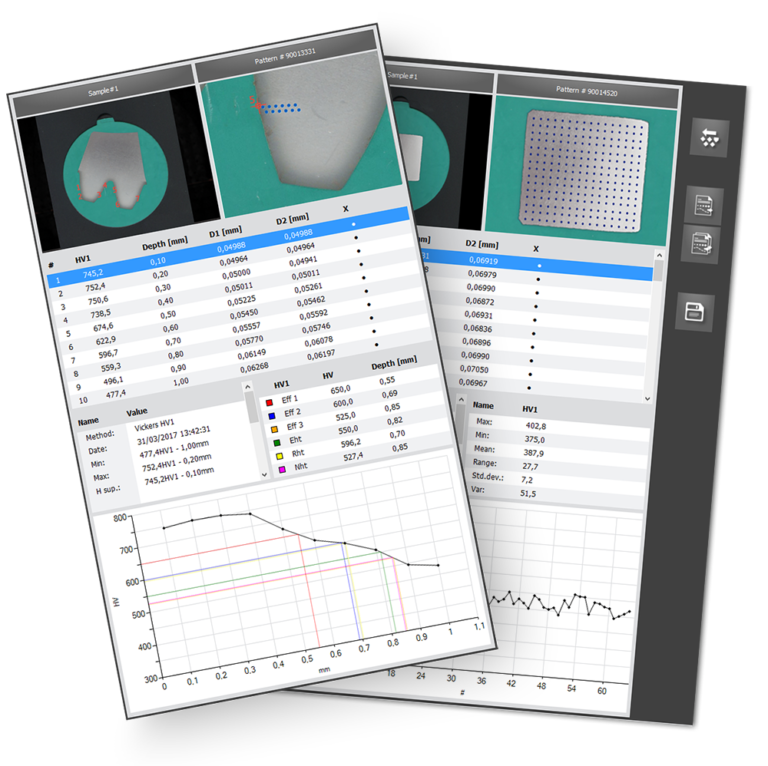
Easy multi Vickers test
CHD TRAVERSES AND PATTERNS
Effortlessly design single or multiple traverses and patterns in no time. A simple click on the line sets the angle and starting point for indentations.
SEMI-AUTOMATIC CHD TESTING
High-precision digital micrometers, connected to the PC, ensure movement resolution with 1 µm steps. The process is guided step-by-step, making it easy to test at the exact XY coordinates required.
CREATE, SAVE, AND RELOAD
Eliminate the hassle of recreating the same pattern repeatedly. This functionality is perfect for users who frequently test similar areas. Once a pattern is designed, it can be saved and reloaded for future use, streamlining analysis on new samples.
MODIFY, REPOSITION, OR DELETE
Select a pattern from the preview image and adjust its direction, location, hardness scale, indentation count and spacing, pattern name, or focal point.
ZOOM IN AND OUT
Zoom out to view the full sample and easily identify the position and orientation of the pattern. Zoom in to inspect pattern spacing and detect surface flaws or imperfections with clarity.
Auto-compensation of all deflections
When examining unstable samples or flexible components, the AFFRI System maintains uninterrupted contact with the specimen, thanks to its unlimited stroke for the indenter and clamping hood. Load forces are delivered via load cells and regulated within a Closed-Loop system operating at a frequency of 1 kHz, ensuring flawless linearity across all ranges. The results remain unaffected by structural deformation, misalignment, or vibrations. This advanced precision guarantees accurate measurements on the first attempt, even under challenging conditions, removing the need for repeat testing. The system’s R&R (Repeatability and Reproducibility) performance is among the highest in its category.
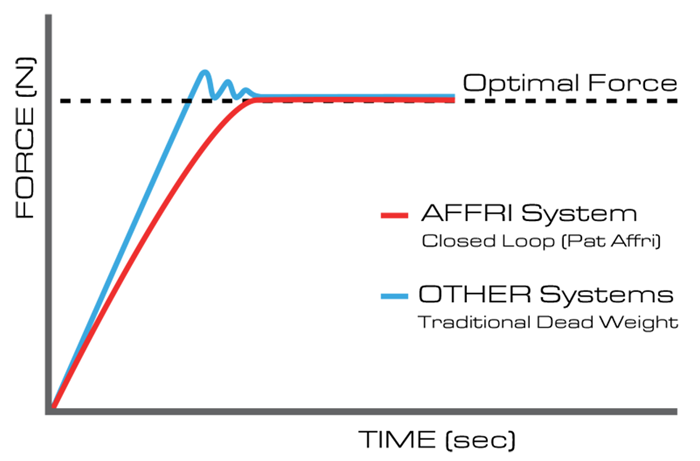
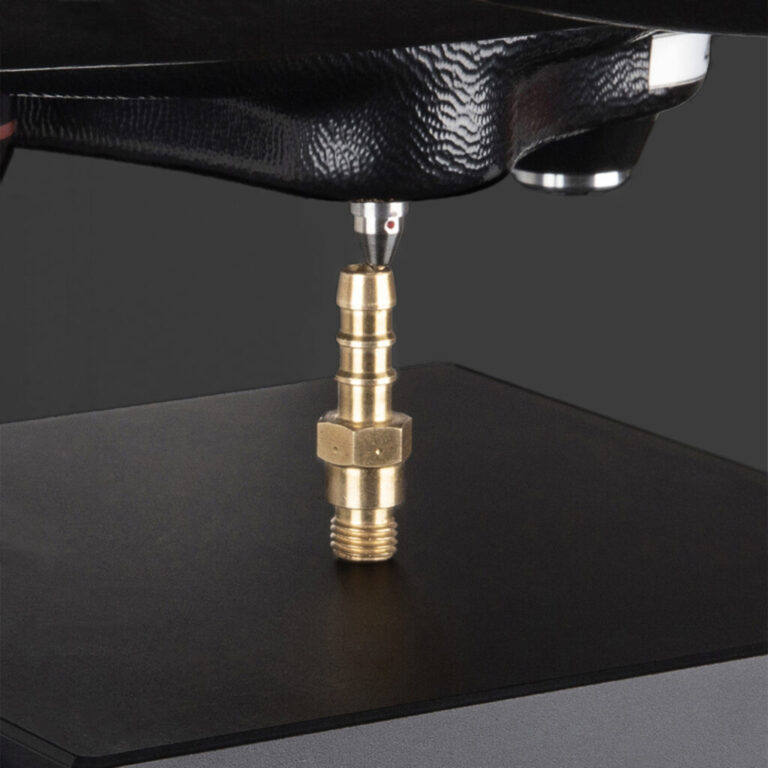
MAIN FEATURES
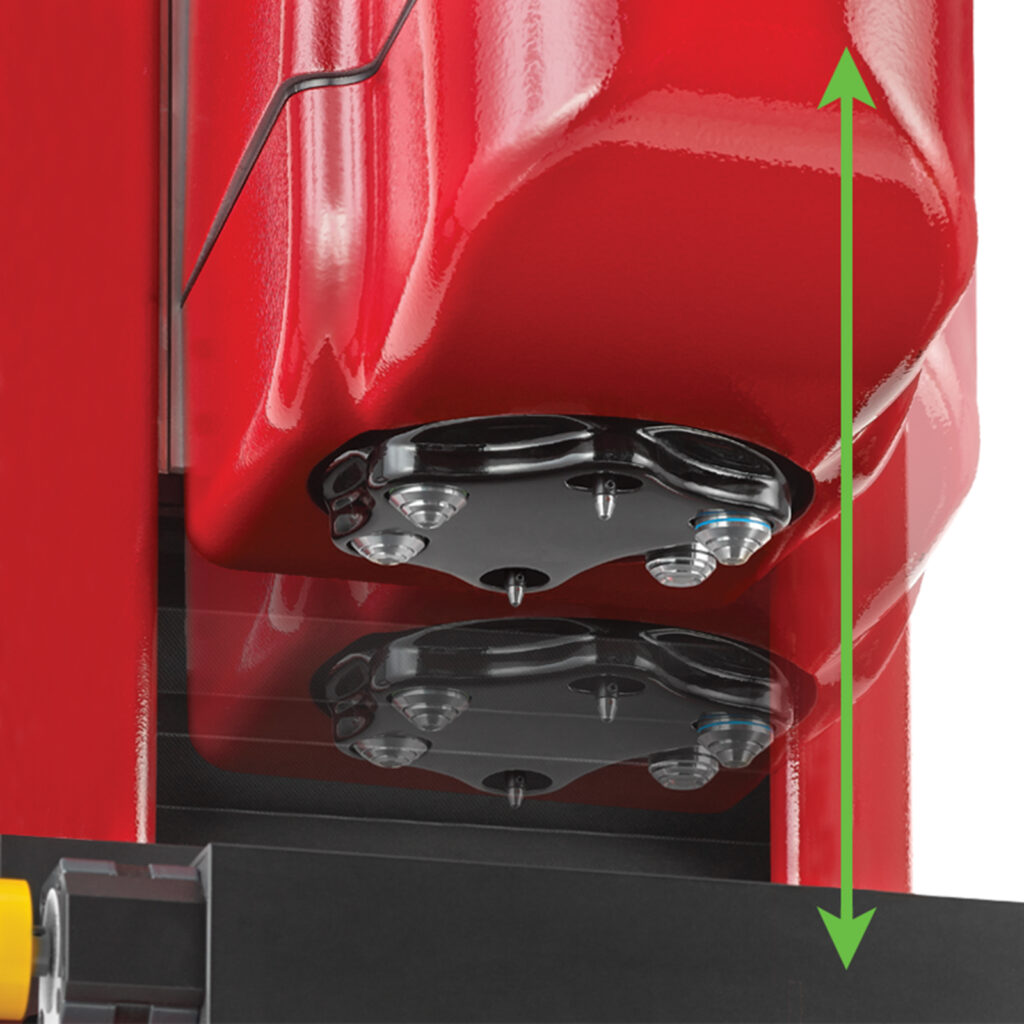
MOTORIZED HEAD
A motorized vertical range of up to 300 mm enables both swift and precise height adjustments. The system features an ultra-responsive and high-speed mechanism, ensuring flawless autofocus accuracy. Paired with fully automated software, it eliminates human interference and significantly enhances repeatability.
MAIN FEATURES
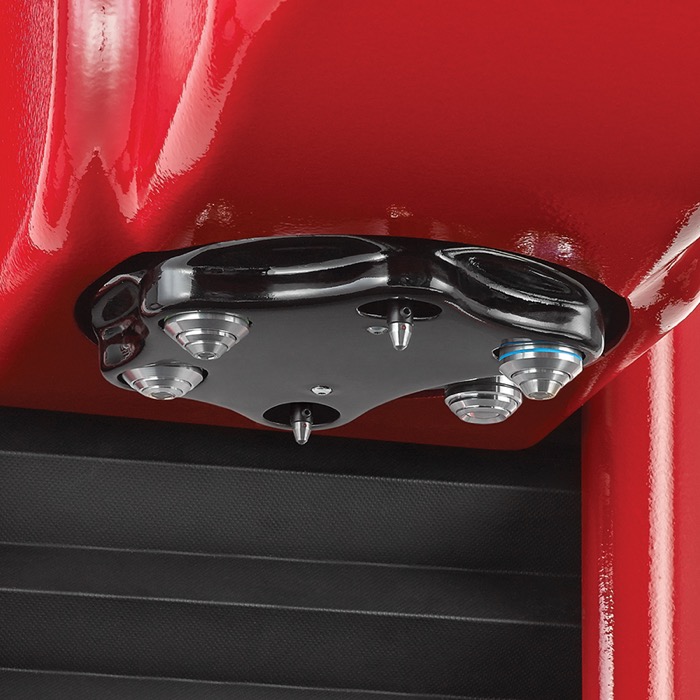
THE MOTORIZED TURRET
The turret rotates horizontally and includes four slots for magnification lenses, two for indenters, and one for a laser pointer. All objectives can be pre-installed and used in conjunction with the indenters for Vickers, Knoop, and Brinell hardness testing scales.
MAIN FEATURES
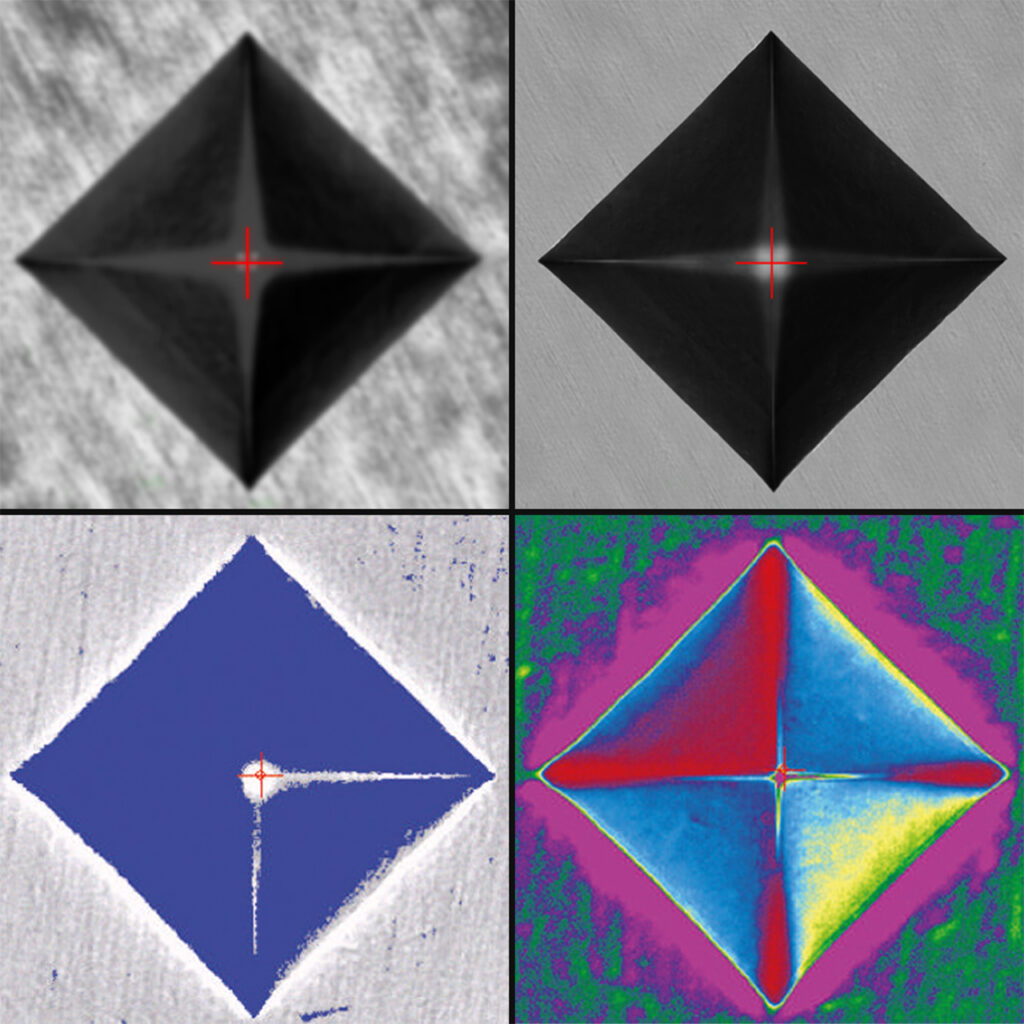
THE AUTOFOCUS
Thanks to the software-controlled focus, image enhancement, shading correction, and regulated lighting, consistent and reproducible results are achieved no matter how many indents are measured. AFFRI WIKI 200’s auto-detection function enables accurate measurements on various sample surfaces, ranging from highly polished to rough or etched materials.
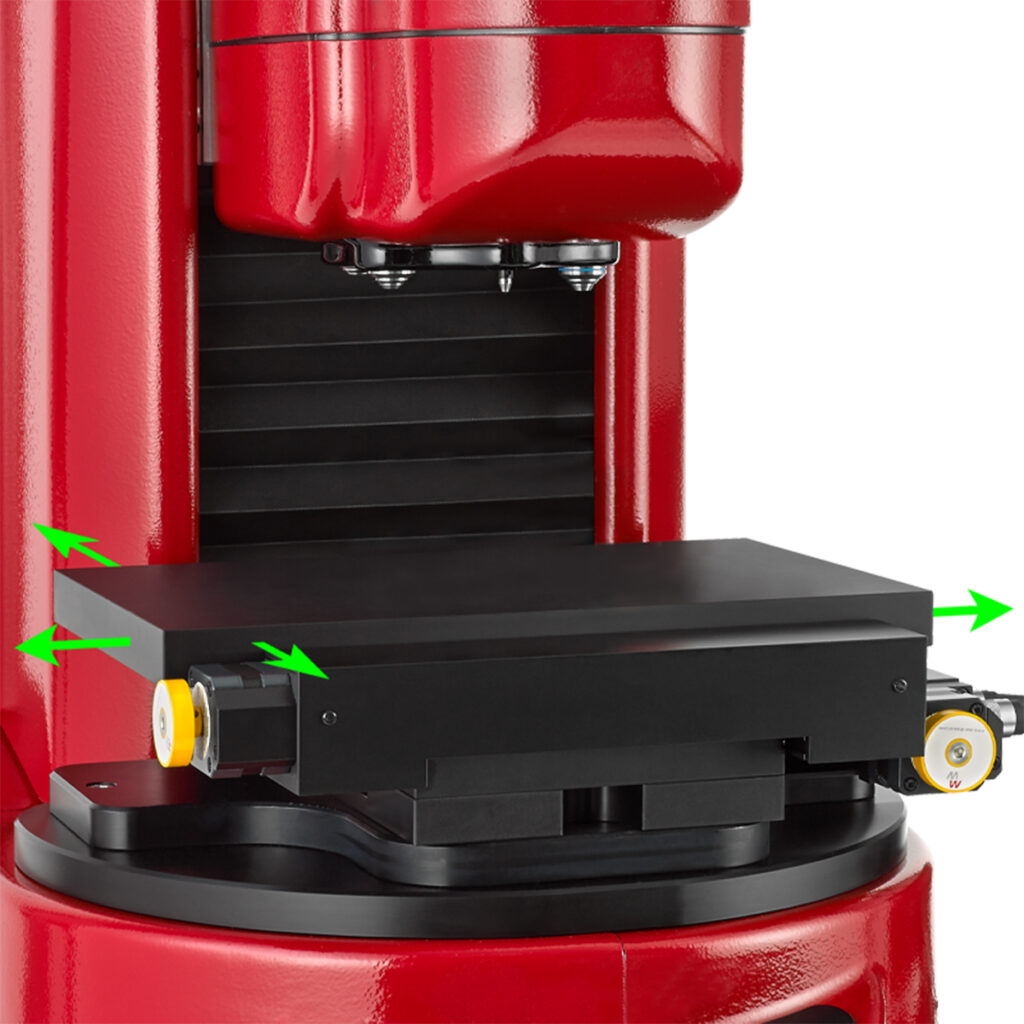
XY MOTORIZED STAGE
The motorized XY table offers precision with steps of +/- 0.5 μm. It facilitates automatic multi-indentation CHD test cycles across multiple samples, ensuring accurate positioning throughout the entire surface, regardless of the number of indentations.
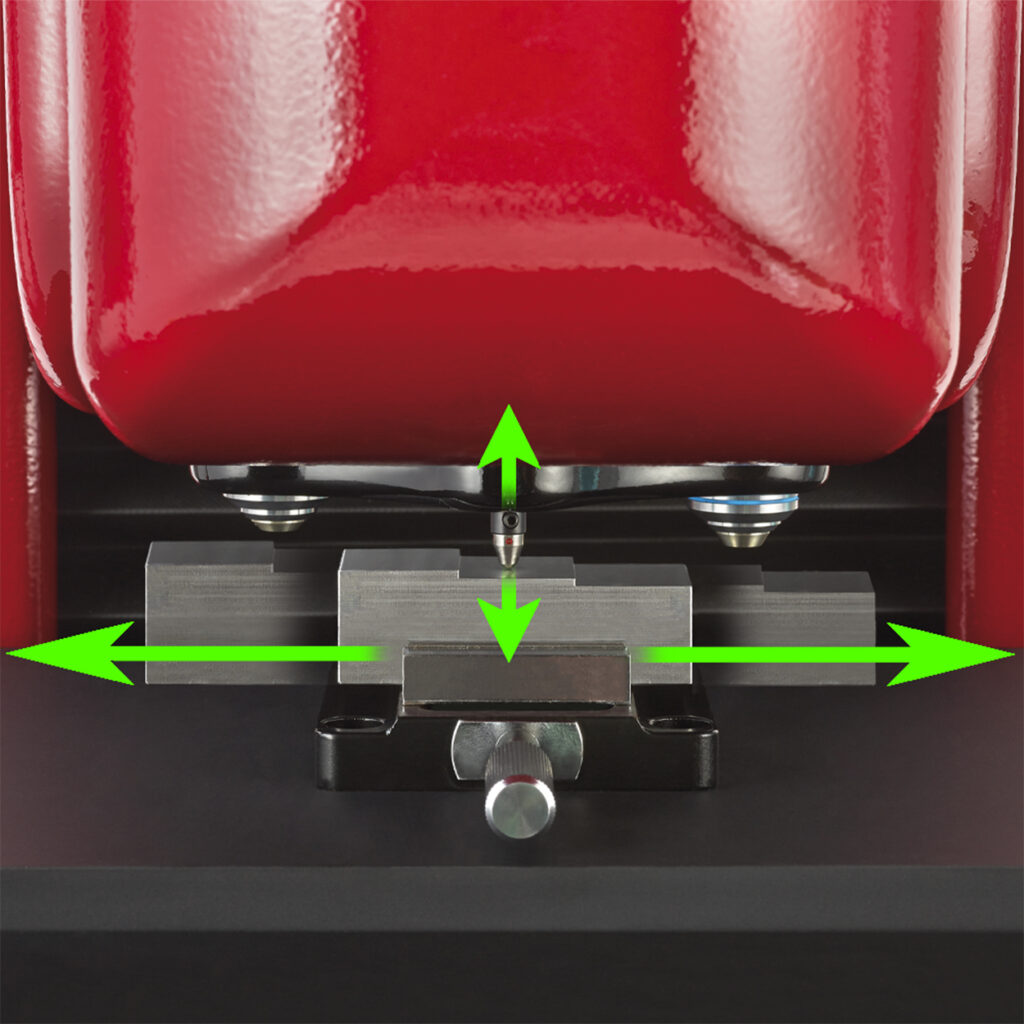
CONTROLLED POSITIONING
Vickers hardness tester AFFRI WIKI 200 is equipped with the automatic surface recognition system. The measuring head makes contact with the sample from any distance and find the correct focus automatically. An anti-collision systemprotects the entire turrets and blocks the tester preventing any accidental damages.
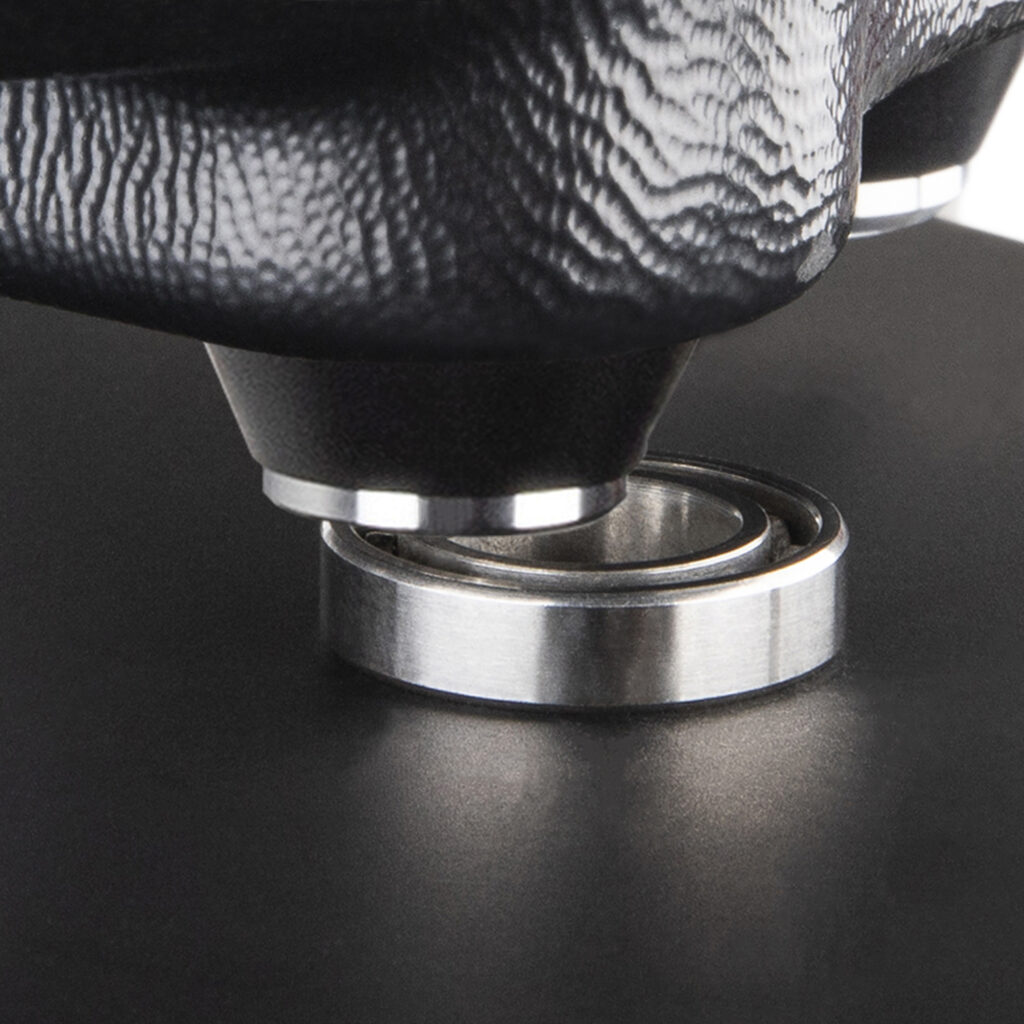
CONTACT TO FOCUS
AFFRI WIKI 200 Vickers hardness tester comes with an automatic surface recognition feature. The measuring head automatically detects the correct focus upon contact with the sample, regardless of distance. Additionally, an anti-collision system safeguards the entire turret, halting the tester to prevent any accidental damage.
Hardness Tests on Wields
Capture a comprehensive panoramic image of the entire weld area, enabling clear identification of the base material, fusion zone, and heat-affected region. The specialized software designed for welding tests allows users to precisely define test paths, setting specific distances between indentations, edges, and various materials in relation to the heat-affected zone. With just a few minutes of analysis, accurate results are generated, offering quick insights into the weld quality and material properties. This efficient system ensures precise measurement with minimal setup time, streamlining the testing process and enhancing overall productivity.
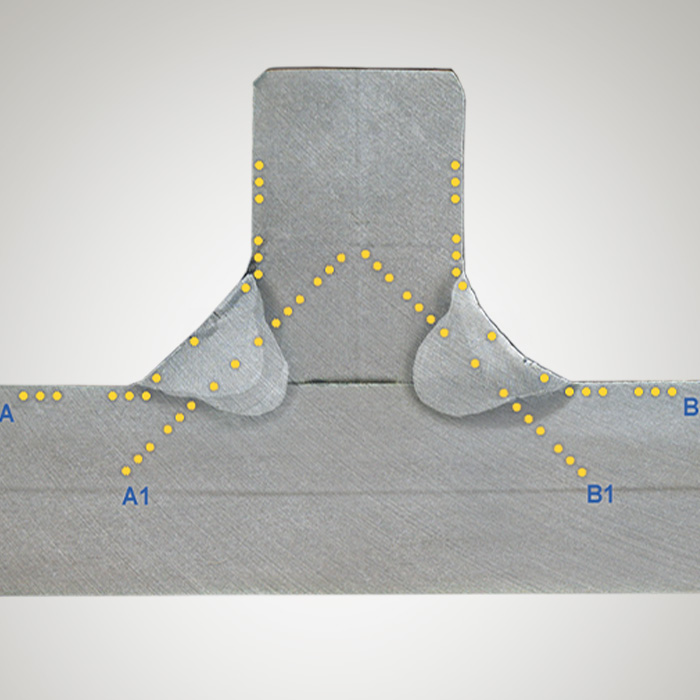