EASYDUR INTEGRAL REVOLVER
Fully Motorized Universal hardness Tester with Multi-position Turret
EASYDUR INTEGRAL REVOLVER is a fully motorized and automatic universal hardness tester with motorized turret at 8 slots : equipped with different hardness scales indenters, different optic lens, laser and a milling station for sample surface preparation before the indentation.
- Test loads from 1 to 3000 kgf (from 9,807 to 29421 N) – As optional from 0,1 kgf (0,9807 N)
- Rockwell ISO 6508 / ASTM E-18: HRA – HRB – HRC – HRD – HRE – HRF – HRG – HRH – HRK – HRL – HRM – HRP – HRR – HRS – HRV HR15N/T/S/W/X/Y – HR30N/T/S/W/X/Y – HR45N/T/S/W/X/Y
- Brinell HBW ISO 6506 / ASTM E-10 HBW1/30 – HBW2.5/15.625 – HBW2.5/31.25 – HBW2.5/62.5 – HBW2.5/187.5 – HBW5/25 – HRW5/62,5 – HBW5/125 – HBW5/250 – HBW5/750 – HBW10/100 – HBW10/250 – HBW10/500 – HBW10/1000 – HBW10/1500 – HBW10/3000 HBWT2.5/62.5 – HBWT2.5/187.5 – HBWT5/125 – HBWT5/250 – HBWT5/750 – HBWT10/500 – HBWT10/1000 – HBWT10/1500 – HBWT10/3000
- BRINELL HBWT ASTM E103 HBWT2.5/62.5 – HBWT2.5/187.5 – HBWT5/125 – HBWT5/250 – HBWT5/750 – HBWT10/500 – HBWT10/1000 – HBWT10/1500 – HBWT10/3000
One Touch Measuremet
EASYDUR INTEGRAL REVOLVER universal hardness tester is a fully motorized system designed for automatic sample loading and optical measurement via camera. System hardness testers provide the highest precision in load application and measurement resolution, setting a new standard in hardness testing. With the System, real indentation measurements are ensured, free from external interference, under all conditions.
How to do a hardness measurement?
The hardness measurements are very easy, quick and absolute. The hardness test cycle is fully automatic and motorized in just one drive (button or icon):
- Automatic contact with the specimen
- Auto-active sliding clamping
- Automatic preloading and loading
- Auto-switching to optic lens
- Autofocus by image scanning brightness
- Auto measure and result display
- Automatic return stroke at programmed distance
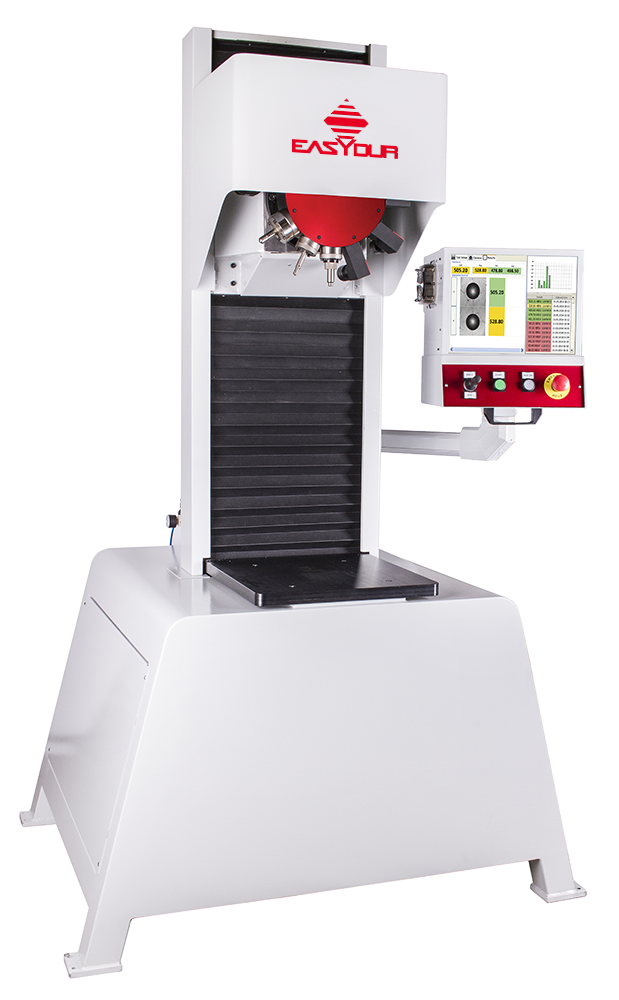
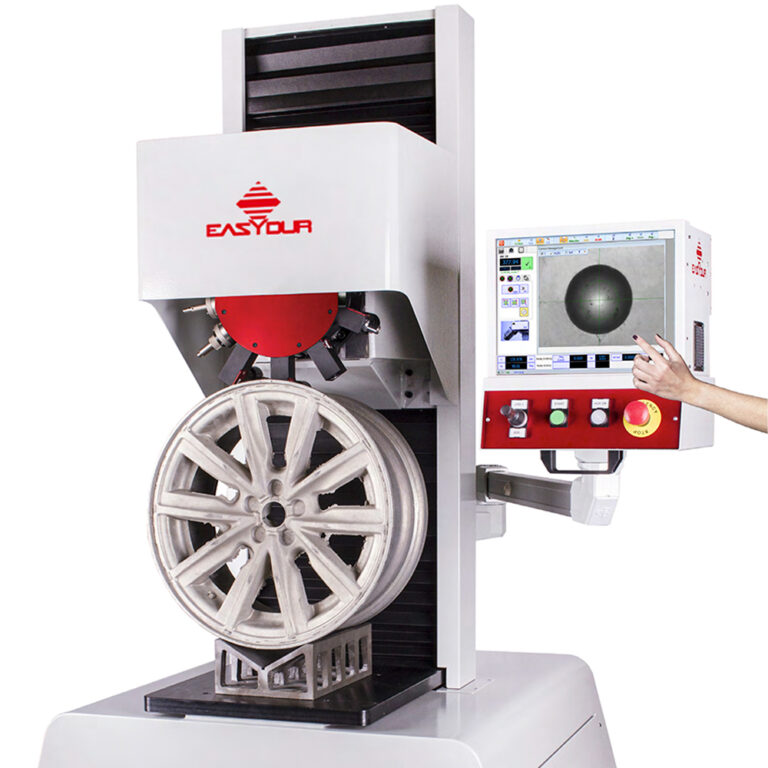
Specimen Auto-contat from any Distance
The fully motorized, adjustable testing stand provides a vertical travel capacity of up to 500 mm / 20″, with automatic surface contact from any distance triggered by a single input. (An optional extension allows up to 700 mm / 28″). The test cycle begins automatically when the head makes contact with the specimen, which is detected at any point within the vertical stroke.
- Vertical capacity from base to the indenter 500mm / 20″ (more on request)
- Horizontal capacity from column to the indenter 280 mm / 11” (more on request)
The Integral hardness tester is a durable system designed for use in tough environments, capable of handling large, heavy samples with a forklift or crane.
Auto-compensation of All Deflections
When testing unstable or deflecting samples, the AFFRI System ensures continuous contact with the specimen, thanks to its infinite stroke capability for both the indenter and clamping hood. This allows the system to track the sample without interruption.
The Closed Loop Control
Load forces are applied via load cells and regulated in a Closed-Loop system with a frequency of 1 kHz, ensuring perfect linearity across all ranges. Structural deflections, misalignments, or vibrations do not affect the results. Precise measurements are achieved on the first test, even under challenging conditions, eliminating the need for repeated trials. The system’s R&R (Repeatability and Reproducibility) data is among the best in its class.

The EXCLUSIVE MILLING TOOL
The Integral Revolver universal hardness tester can be fitted with a sample preparation system that is directly mounted on the instrument’s head.
- Save time! Only 30 seconds to get the Brinell result!
- Increase the accuracy and the quality of your Brinell results
- Automatize the quality inspection process
- Move human resources to other jobs
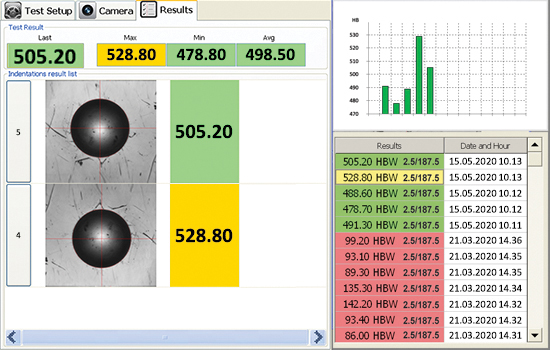
Software
EASYDUR INTEGRAL REVOLVER universal hardness tester comes with pre-installed software that manages the entire testing process, minimizing the risk of operator errors.
- 15″ Touchscreen
- Intuitive, user-friendly interface
- Color-coded result indicators (low/ok/high)
- Real-time statistics and graphical displays
- Customizable test settings programs
- Result archiving
- Image capture and storage
- Export results in various formats including PDF, TXT, CSV, DOC, XLS, and more
- Barcode scanning for data input
- Output options via RS232, USB, and Ethernet
- Seamless data exchange with MES management systems.
9-Position Turret
The pneumatic turret offers 360° rotation with 9 selectable positions for objectives and indenters. The indenters and optical lenses automatically interchange, adapting seamlessly to various hardness testing methods. The multiple objectives ensure precise and consistent indentation scanning. The turret also includes a milling head that automatically prepares the surface prior to testing.
Milling
The integrated milling head automatically prepares the test surface, ensuring optimal results with every measurement.
L.I.S.A.
The laser pointer (AFFRI® Pat.) precisely defines the testing area before the indenter engages the workpiece, enabling accurate measurements on challenging surfaces such as gear teeth, sharp edges, and irregular contours.
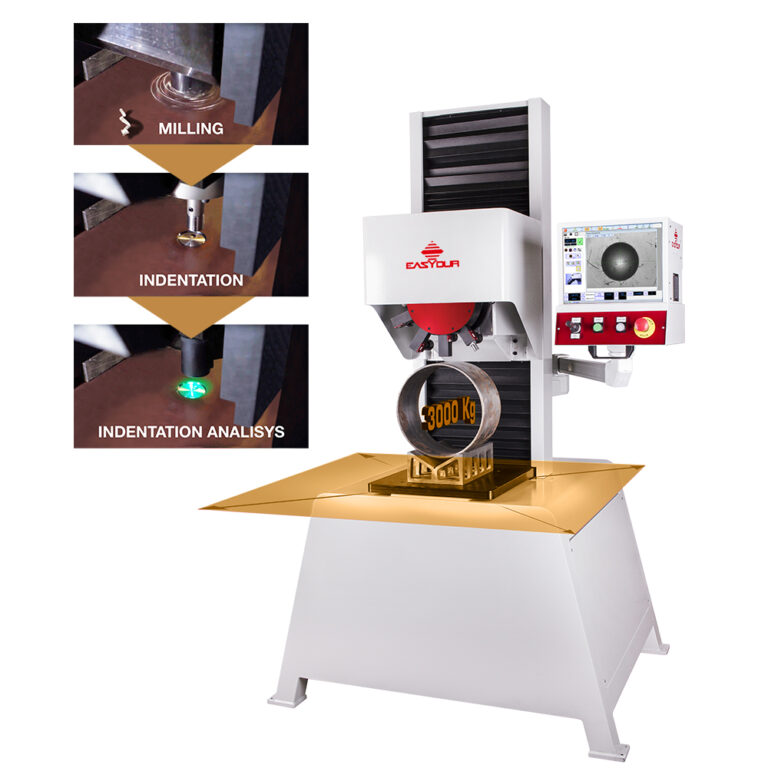
MAIN FEATURES
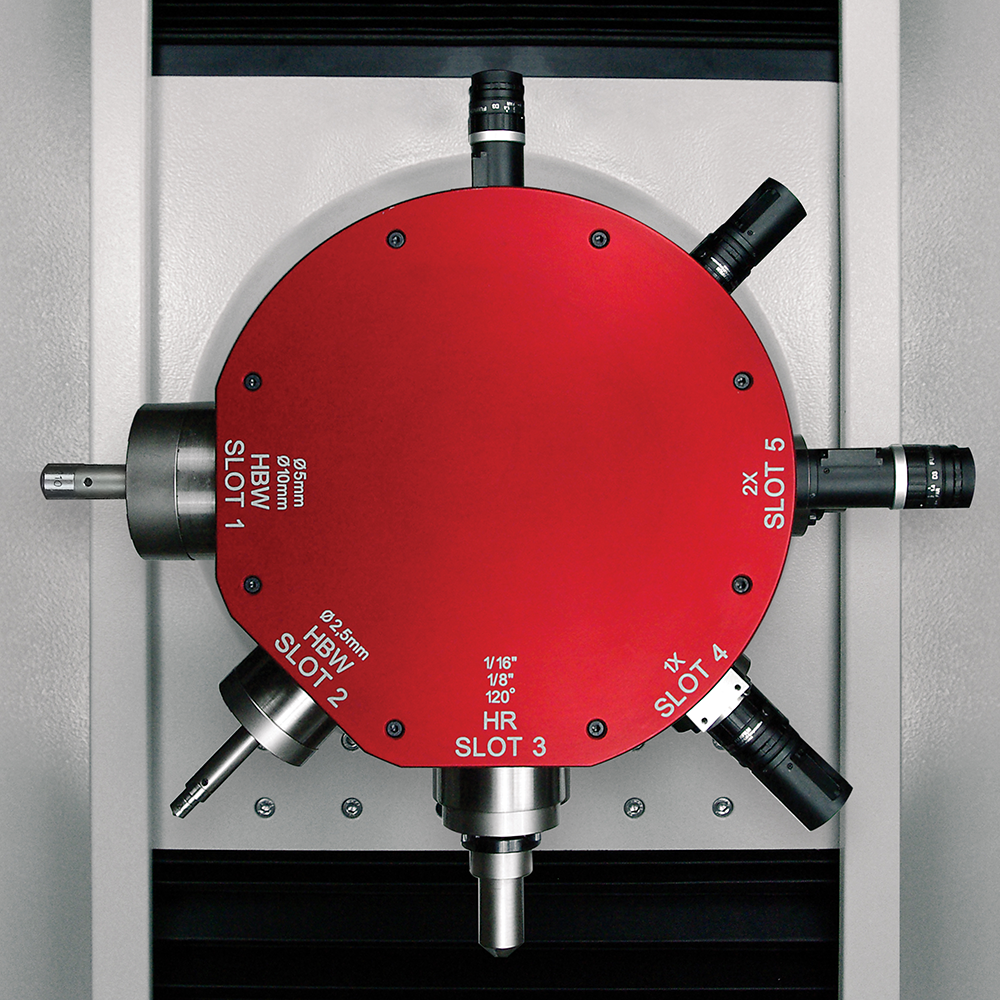
MOTORIZED TURRET
The turret can accommodate up to 8 slots (or more) for various hardness scale indenters, optical lenses, lasers, and even a milling tool for surface preparation. It features auto-rotation and auto-tool switching, enabling a fully automated measurement cycle. This setup allows for both single and multi-method hardness testing using a single instrument.
MAIN FEATURES
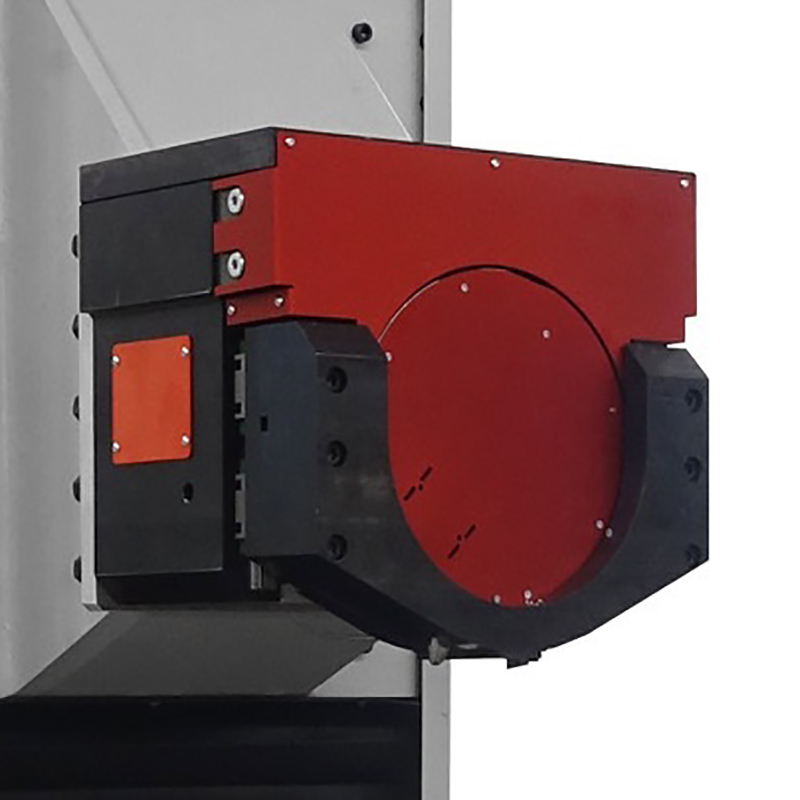
CLAMPING SYSTEM
A secure connection with the specimen is consistently maintained, even in the rare case of any movement during the test cycle. The clamping system guarantees full stability of the test piece throughout the entire process, regardless of its whether condition oiled, rusty, or contaminated with dirt.
MAIN FEATURES
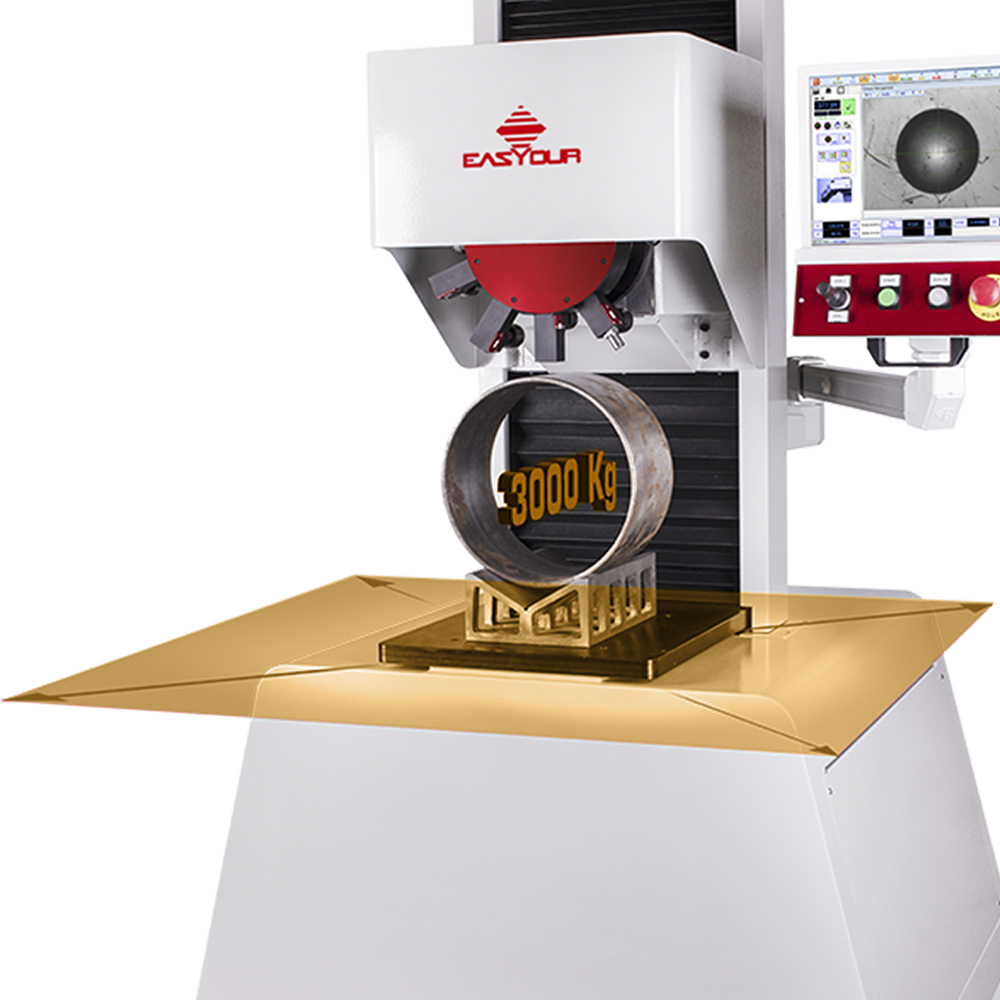
HARD BASE
The spacious worktable base is designed to support weights exceeding 3000 kg, along with specialized fixtures or anvils. It allows for hardness testing of large and irregularly shaped specimens that are difficult to accommodate with standard bench hardness testers.
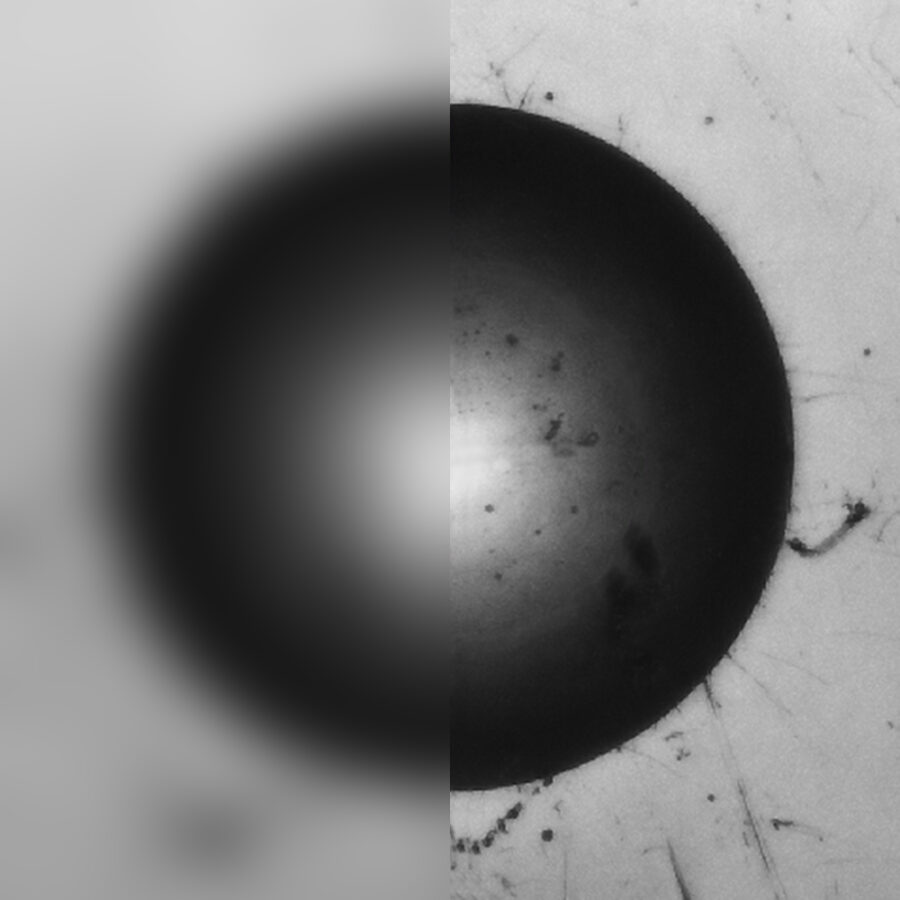
AUTOFOCUS
The automatic focus adjustment system for each optic ensures precise positioning at any magnification, utilizing real image brightness scanning with continuous steps for infinite accuracy. This technology guarantees high reading standards, reproducible focus values, and reduces reading time. Hardness measurements remain objective, unaffected by subjectivity.
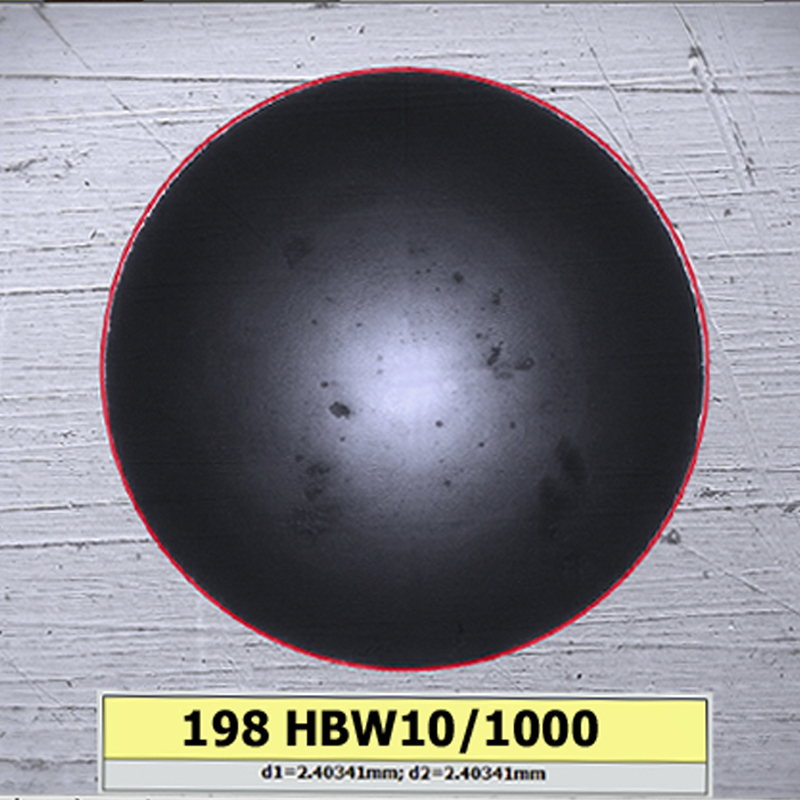
CAMERA AUTO-READING
The software automatically measures indentations on any sample surface, ranging from perfectly polished to rough or etched materials. It features automatic light regulation for dark, opaque, or polished samples, adjusting both light and contrast to optimize visibility and ensure accurate indentation measurements.
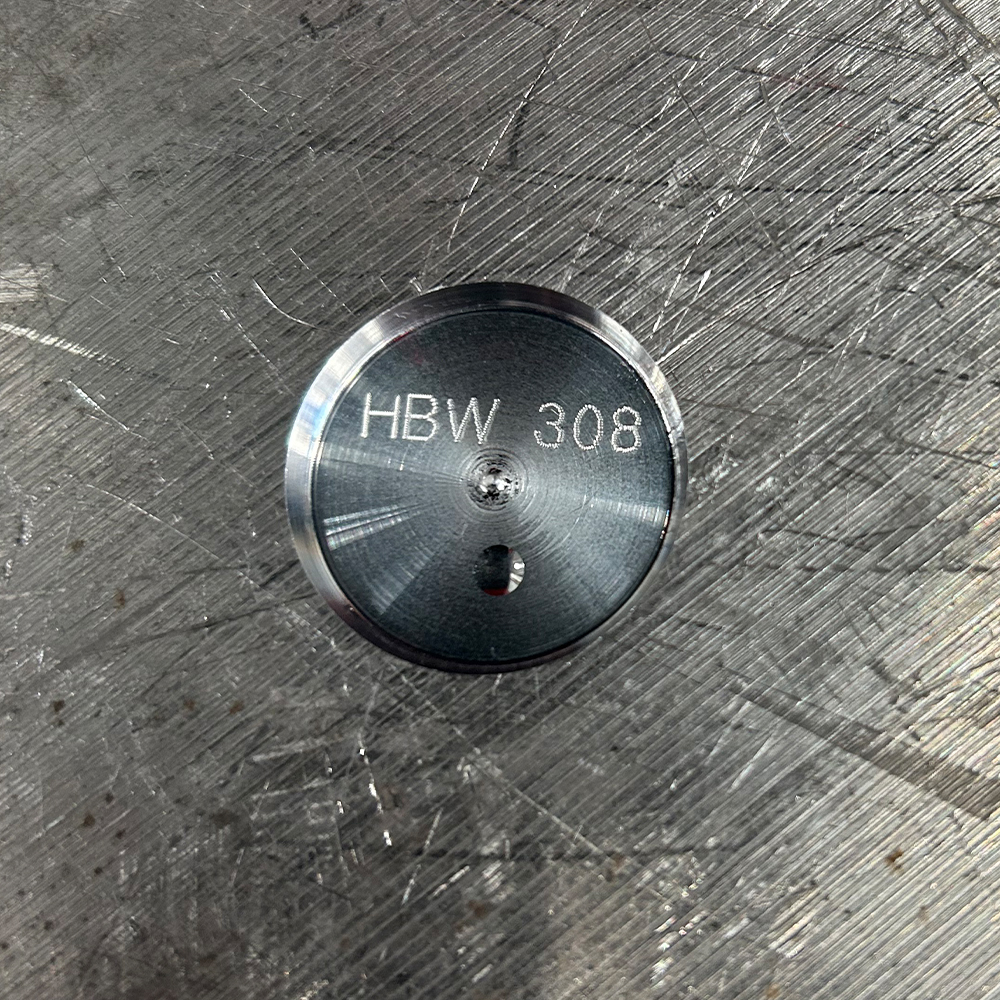
SAMPLE SURFACE PREPARATION BY MILLING
The INTEGRAL system features an integrated milling tool for sample preparation, installed directly within the instrument head. This milling station is one of the 9 positions in the head, and it automatically operates to ensure precise measurements in just a few seconds.