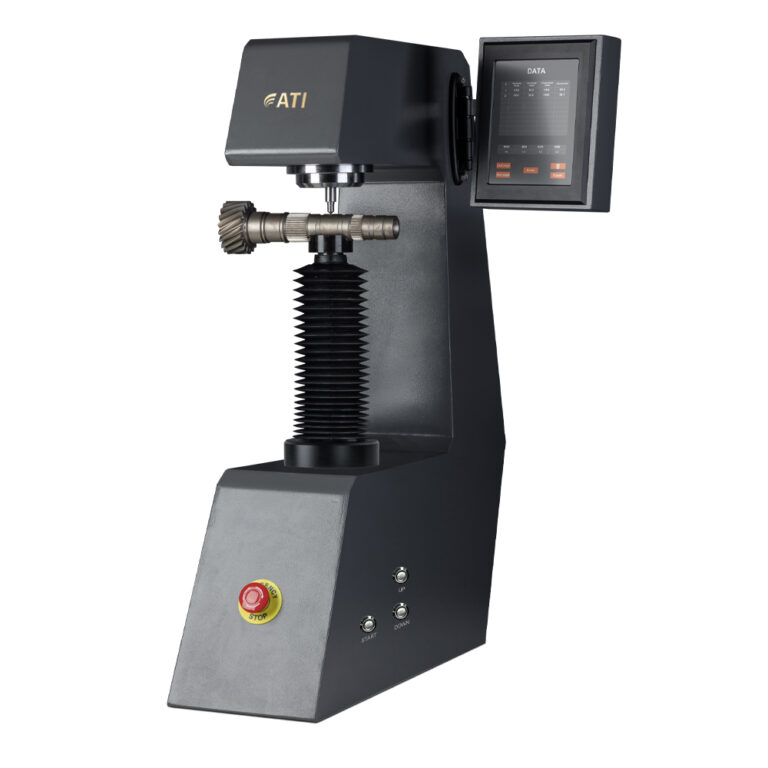
ATI MRS
Motorized and Automatic Rokwell and Superficial Rockwell hardness tester
ATI MRS is a Motorized and Automatic Rockwell and Superficial Rockwell Hardness Tester, engineered to meet the rigorous standards set forth by ASTM E18, ISO 6508, and ISO 2039-2. This advanced testing instrument employs a high-precision load cell and Closed-Loop electronic control with a 1 KHz sampling rate, ensuring optimal accuracy and reliability.
The automatic start test cycle is initiated with a single input command, streamlining the testing process and enhancing efficiency.
ATI MRS is designed to accurately measure the hardness of ferrous, non-ferrous metals, and non-metal materials. Engineered for high accuracy, this tester meets the needs of manufacturers and engineers who require precise hardness measurements in critical applications.
CLAMPING SYSTEM
Thanks to the workpiece press hood, it is possible to perform measurements in complete safety even on particularly unstable samples, ensuring optimal stability during the testing process. Furthermore, the hood allows the measurement point to be precisely visualized, ensuring that each operation is performed correctly and without risks for the operator or the sample.
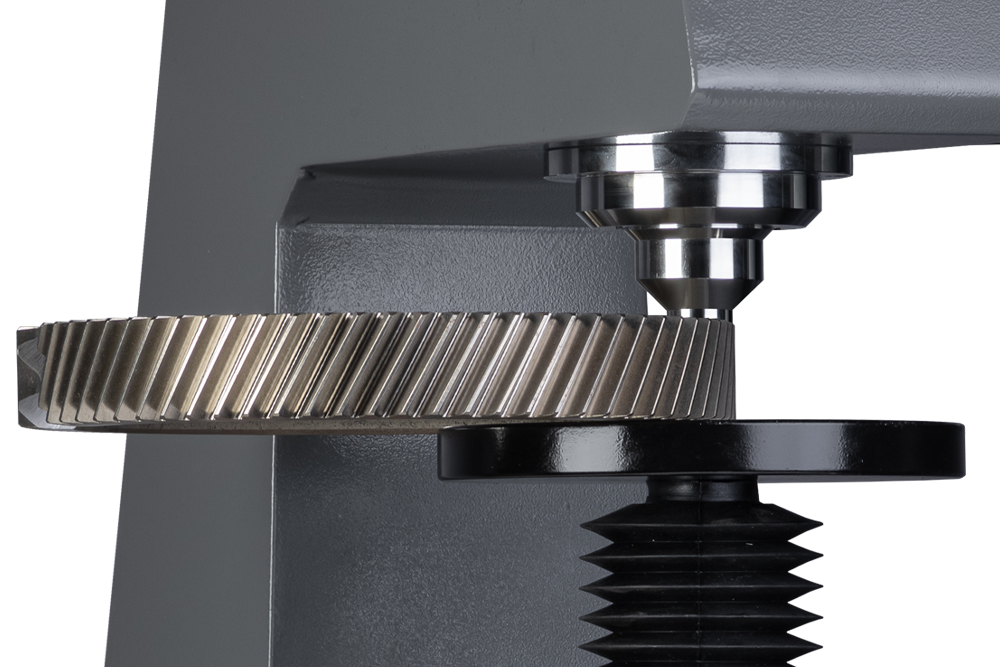
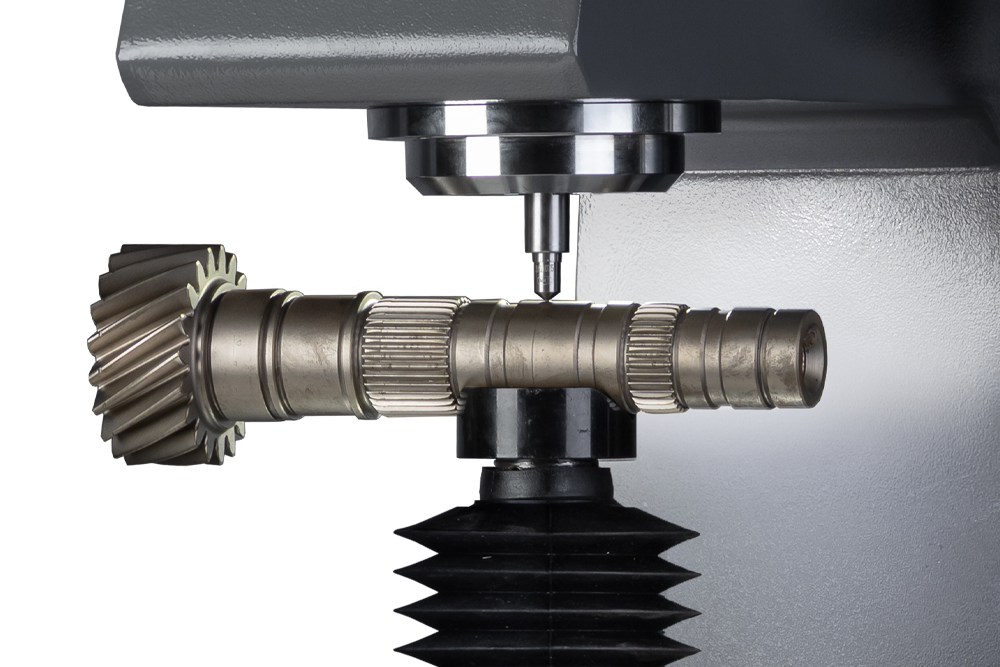
TESTING AREA
ATI MRS is the result of a study aimed at improving the testing experience. We have designed a work area lighting that guarantees excellent visibility of the most difficult measurement points, thus facilitating the operator and reducing the probability of measurement errors or breakage of the penetrators, helping to extend their life. The lighting is rechargeable directly on board the machine via a USB port. We have also designed an innovative work area, with a maximum test height of up to 290 mm and a depth of 210 mm.
AUTOMATED MEASUREMENT CYCLE
To start the hardness test, simply press the START button. The motorized lifting screw will bring the sample to the test area. Contact with the sample, preload, load and measurement occur automatically. During the process, the operator can monitor in real time on the screen each single phase of the test cycle. At the end of the measurement, the result is provided automatically.
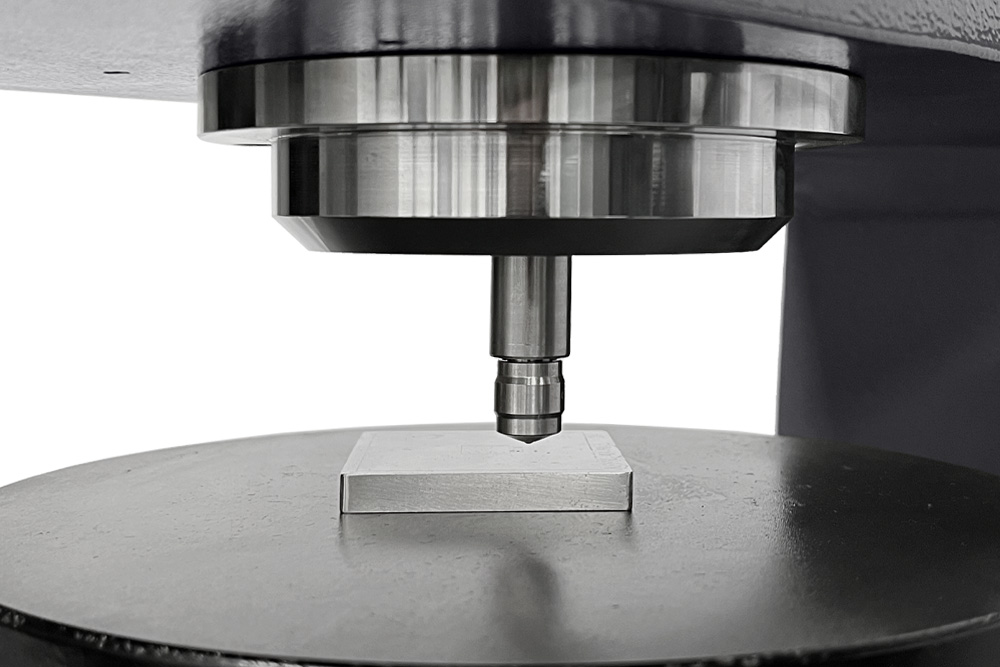
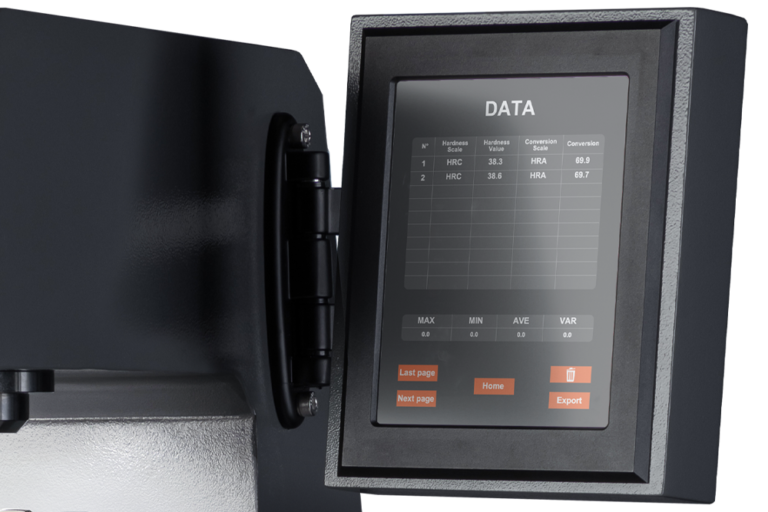
CONTROL PANEL
The control panel is positioned laterally and can be easily moved using an adjustable articulated arm support, which allows it to be moved backwards or forwards based on specific movement needs during use of the instrument. This feature offers great versatility, allowing the operator to optimize the visibility of the screen and, at the same time, adapt the position of the panel to facilitate access and management of the parts. In addition, by moving the panel, it is possible to increase the work area to accommodate bulkier parts, improving overall efficiency during operations.
FUNCTIONAL BASE
The structure of the ATI MRS has been developed to maximize hardness testing: the buttons at the base make the measurement automatic and motorized. This simplifies the operator’s work, increasing accuracy and reducing the risk of errors. Furthermore, no preparation of holes in the support table is necessary, since the lifting screw is entirely contained within the base, avoiding the need to drill holes in the support bench. Thus, the hardness tester can be freely positioned where most convenient, without compromising the stability of the system.
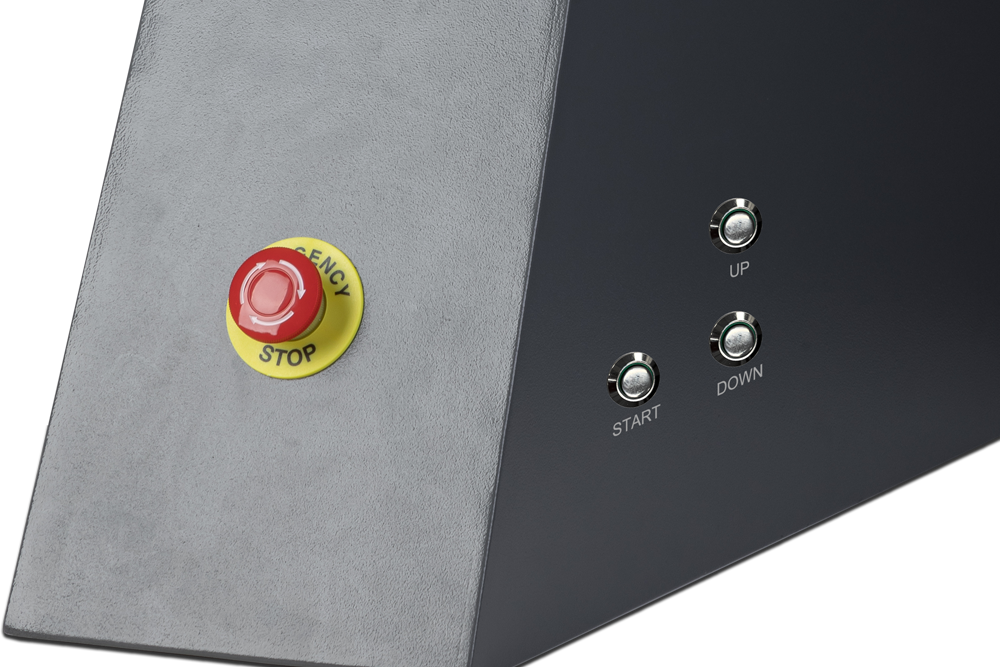
SOFTWARE
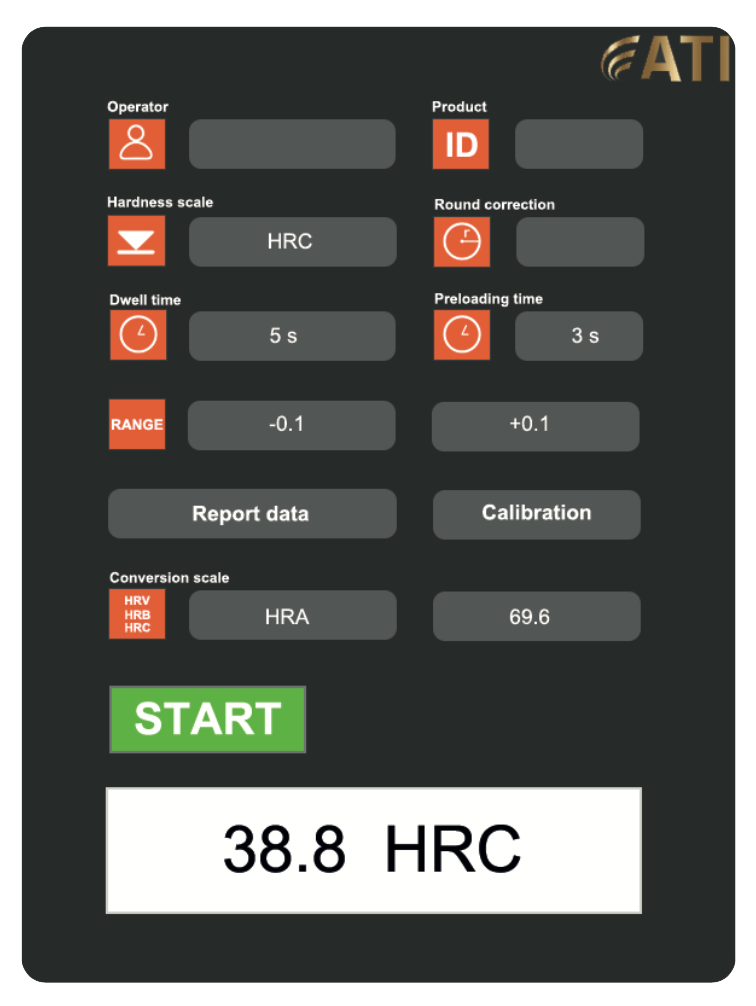
CUSTOM TEST SETTINGS
The user can set standard measurement values with customized acceptance limits based on the specific requirements of the product. This allows to quickly determine whether a product passes or fails the control based on the predefined thresholds. It is also possible to set the name of the operator, the product codes, the dwell times in the measurement phases, the conversion of the values into other scales, as well as the correction values for measurements on cylindrical surfaces. In addition, statistics can be set and the collected data can be stored.
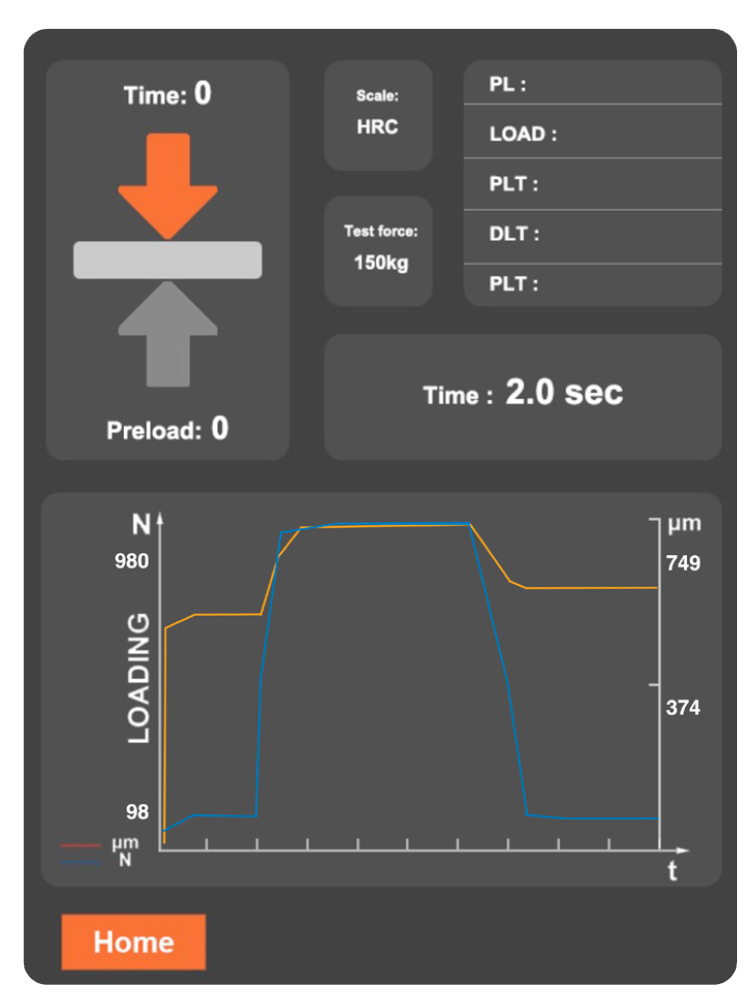
REAL-TIME VIEW
The operator has full control of the process. The large, high-definition, multi-color graphic display shows each phase of the test cycle in real time through a graph representing the preload cycle, the load, and the dwell times. At the end of the test, the result appears and changes color based on the set acceptability thresholds: green (perfect), red (out of limits), yellow (within limits). In this way, it is possible to verify whether the hardness measurement is within the established limits. A diagram representing the relationship between the applied forces and the imprint is also available.
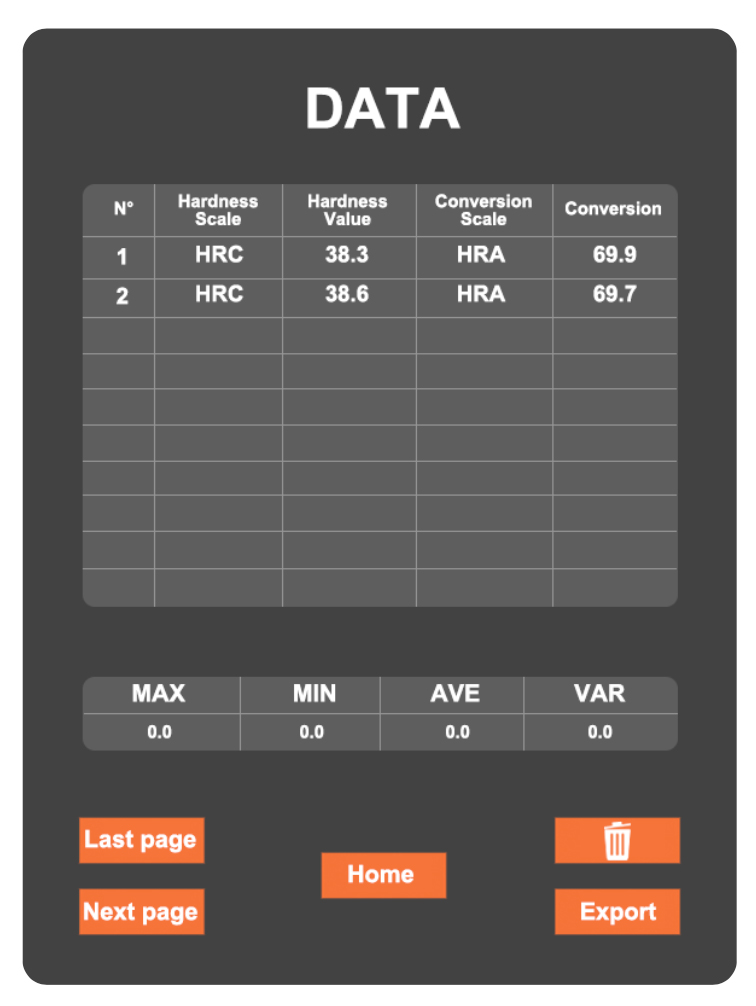
DATA CONVERSION AND STATISTICS
In addition to the measurement result, it is possible to consult the conversion values in the various selected scales, view the statistics and manage the data. Before carrying out the hardness tests, it is possible to insert a flash memory into the USB port, which will record all the data detected during the measurements and sort them in XML format. The data can then be exported, saved on an external PC, sent to a printer or transmitted over the network.
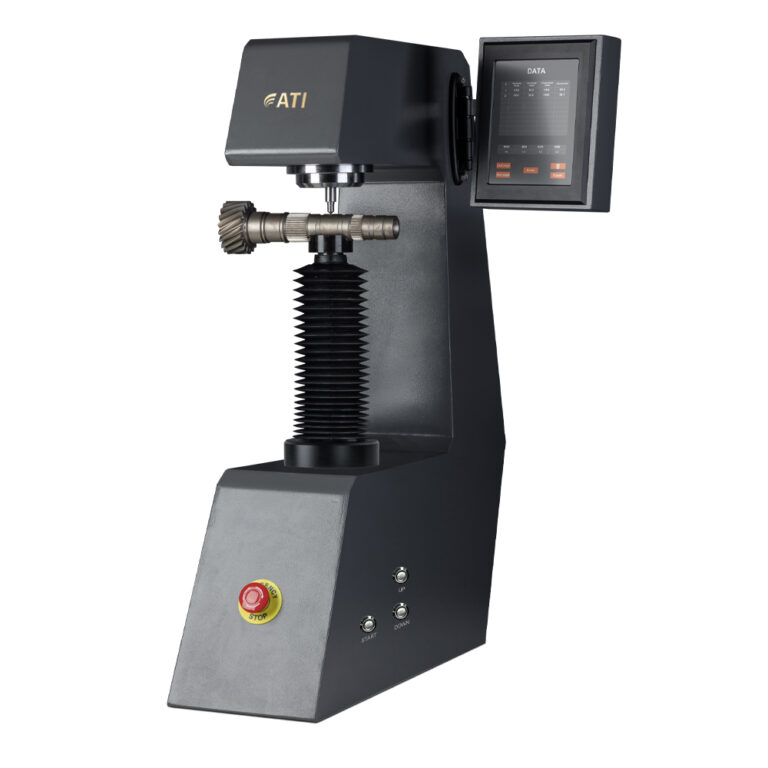
ATI MRS
Motorized and automatic Rockwell and Superficial Rockwell hardness tester
ATI MRS is a Motorized and Automatic Rockwell and Superficial Rockwell Hardness Tester, engineered to meet the rigorous standards set forth by ASTM E18, ISO 6508, and ISO 2039-2. This advanced testing instrument employs a high-precision load cell and Closed-Loop electronic control with a 1 KHz sampling rate, ensuring optimal accuracy and reliability.
The automatic start test cycle is initiated with a single input command, streamlining the testing process and enhancing efficiency. ATI MRS is designed to accurately measure the hardness of ferrous, non-ferrous metals, and non-metal materials. Engineered for high accuracy, this tester meets the needs of manufacturers and engineers who require precise hardness measurements in critical applications.
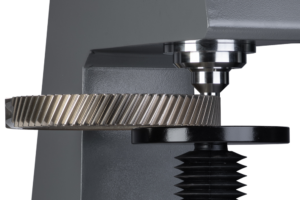
CLAMPING SYSTEM
Thanks to the workpiece press hood, it is possible to perform measurements in complete safety even on particularly unstable samples, ensuring optimal stability during the testing process. Furthermore, the hood allows the measurement point to be precisely visualized, ensuring that each operation is performed correctly and without risks for the operator or the sample.
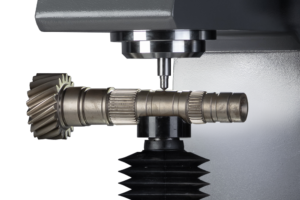
TESTING AREA
ATI MRS is the result of a study aimed at improving the testing experience. We have designed a work area lighting that guarantees excellent visibility of the most difficult measurement points, thus facilitating the operator and reducing the probability of measurement errors or breakage of the penetrators, helping to extend their life. The lighting is rechargeable directly on board the machine via a USB port. We have also designed an innovative work area, with a maximum test height of up to 290 mm and a depth of 210 mm.
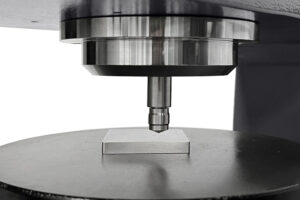
AUTOMATED MEASUREMENT CYCLE
To start the hardness test, simply press the START button. The motorized lifting screw will bring the sample to the test area. Contact with the sample, preload, load and measurement occur automatically. During the process, the operator can monitor in real time on the screen each single phase of the test cycle. At the end of the measurement, the result is provided automatically.
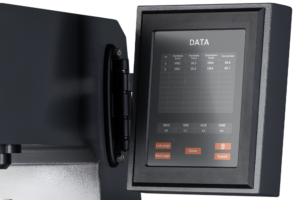
CONTROL PANEL
The control panel is positioned laterally and can be easily moved using an adjustable articulated arm support, which allows it to be moved backwards or forwards based on specific movement needs during use of the instrument. This feature offers great versatility, allowing the operator to optimize the visibility of the screen and, at the same time, adapt the position of the panel to facilitate access and management of the parts. In addition, by moving the panel, it is possible to increase the work area to accommodate bulkier parts, improving overall efficiency during operations.
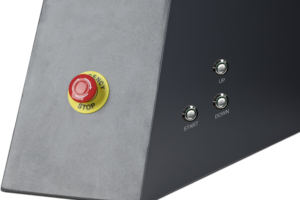
FUNCTIONAL BASE
The structure of the ATI MRS has been developed to maximize hardness testing: the buttons at the base make the measurement automatic and motorized. This simplifies the operator’s work, increasing accuracy and reducing the risk of errors. Furthermore, no preparation of holes in the support table is necessary, since the lifting screw is entirely contained within the base, avoiding the need to drill holes in the support bench. Thus, the hardness tester can be freely positioned where most convenient, without compromising the stability of the system.
SOFTWARE
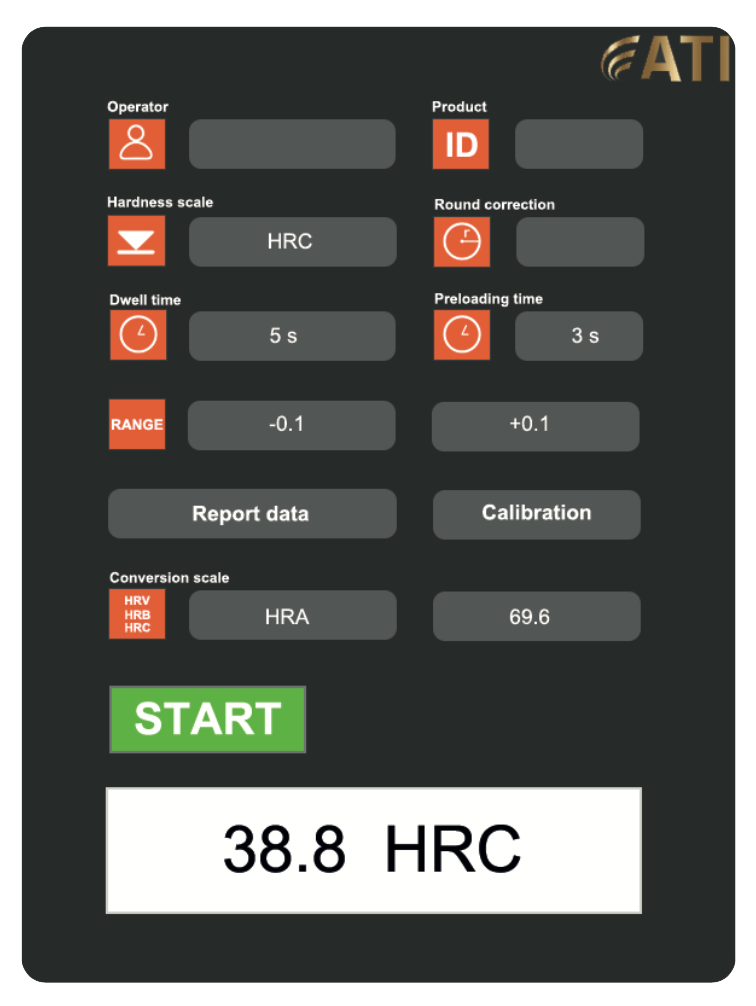
CUSTOM TEST SETTINGS
The user can set standard measurement values with customized acceptance limits based on the specific requirements of the product. This allows to quickly determine whether a product passes or fails the control based on the predefined thresholds. It is also possible to set the name of the operator, the product codes, the dwell times in the measurement phases, the conversion of the values into other scales, as well as the correction values for measurements on cylindrical surfaces. In addition, statistics can be set and the collected data can be stored.
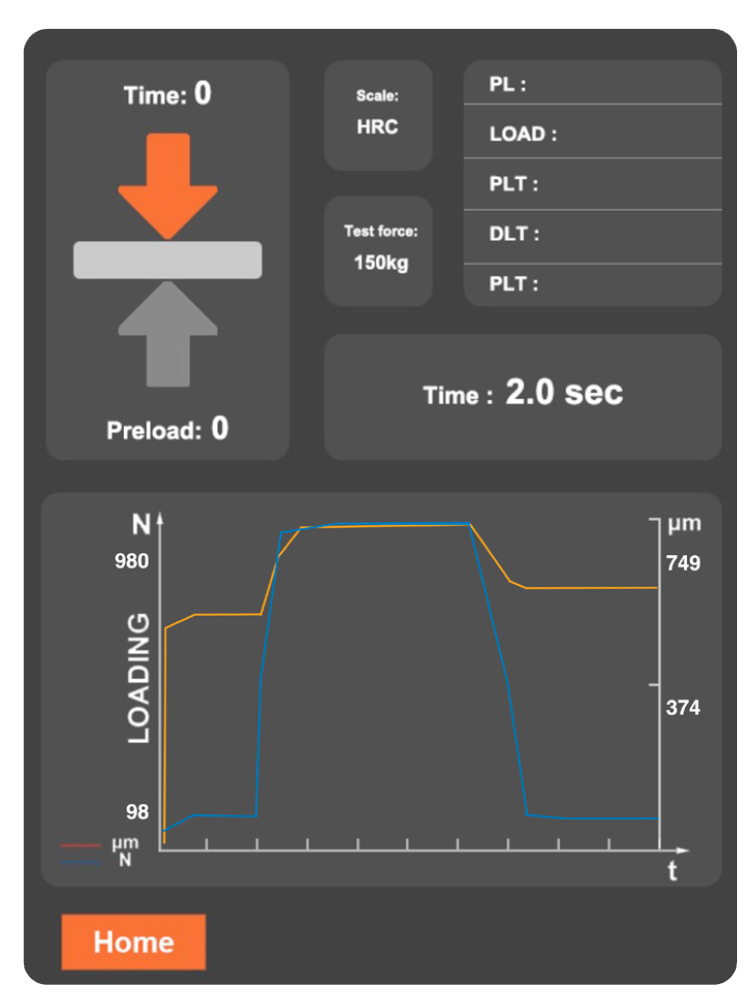
REAL-TIME VIEW
The operator has full control of the process. The large, high-definition, multi-color graphic display shows each phase of the test cycle in real time through a graph representing the preload cycle, the load, and the dwell times. At the end of the test, the result appears and changes color based on the set acceptability thresholds: green (perfect), red (out of limits), yellow (within limits). In this way, it is possible to verify whether the hardness measurement is within the established limits. A diagram representing the relationship between the applied forces and the imprint is also available.
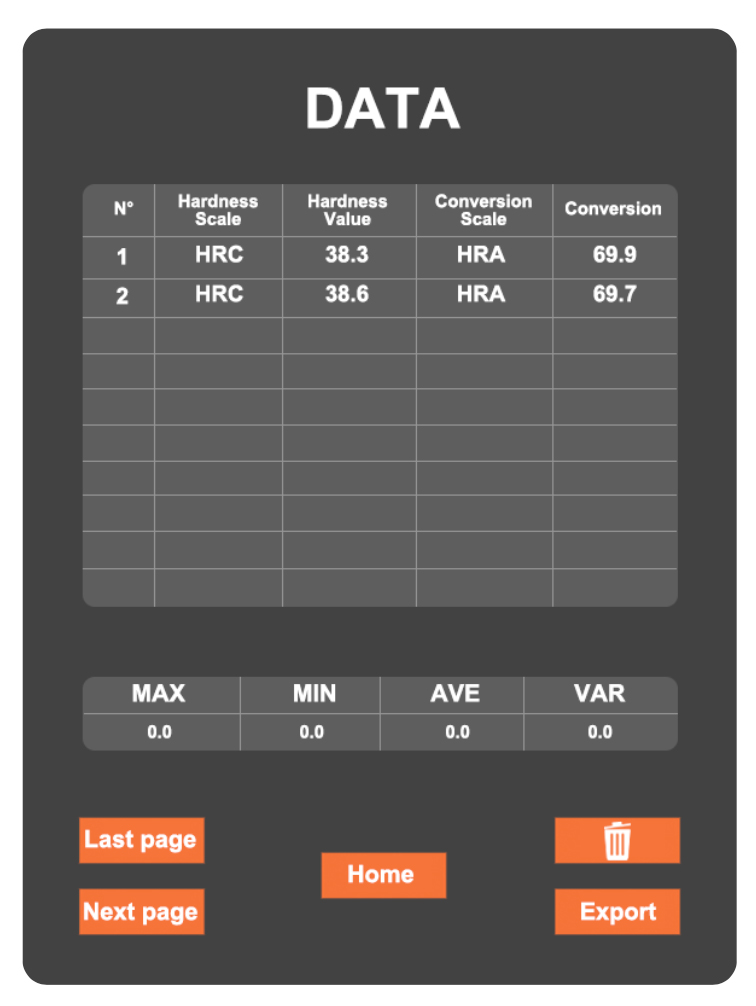
DATA CONVERSION AND STATISTICS
In addition to the measurement result, it is possible to consult the conversion values in the various selected scales, view the statistics and manage the data. Before carrying out the hardness tests, it is possible to insert a flash memory into the USB port, which will record all the data detected during the measurements and sort them in XML format. The data can then be exported, saved on an external PC, sent to a printer or transmitted over the network.
Model: | ATI MRS |
Compliance standards: | ASTM E18, ISO 6508 and ISO 2039-2 |
Hardness scales: | HRA, HRD, HRC, HRF, HRB, HRG, HRH, HRE, HRK, HRL, HRM, HRP, HRR, HRS, HRV, HRX, HRS, HBWT 2,5/62,5- HBWT 2,5/187,5- HBWT 5/250 |
Conversion scales: | HV, HK, HRA, HRB, HRC, HRD, HRE, HRF, HRG, HRK, HR15N, HR30N, HR45N, HR15T, HR30T, HR45T, HS,HBW |
Initial test force: | 3 Kg (29.42 N), 10 Kg (98.07 N) |
Rockwell test force: | 15 Kg (147.1 N), 30 Kg (294.2 N), 45 Kg (441.3 N), 60 Kg (588.4 N), 100 Kg (980.7 N), 150 Kg (1471 N) |
Brinell test force: | 62.5 Kg (613N), 187.5 Kg (1839.4 N), 250 Kg (2452 N) (at request) |
Vickers test force: | 3 Kg (29.41 N), 5 Kg (49.03 N), 10 Kg (98.07 N), 30 Kg (294.2 N), 60 Kg (588.4 N), 100 Kg (980 N) (at request) |
Dwell time: | Adjustable from 2 to 60 seconds |
Height capacity: | 270 mm |
Depth capacity of throat: | 205 mm |
Power supply: | 220V / 110V , 50 Hz / 60 Hz |
Data output: | USB |
Total dimensions: | 475 x 200 x 700 mm |