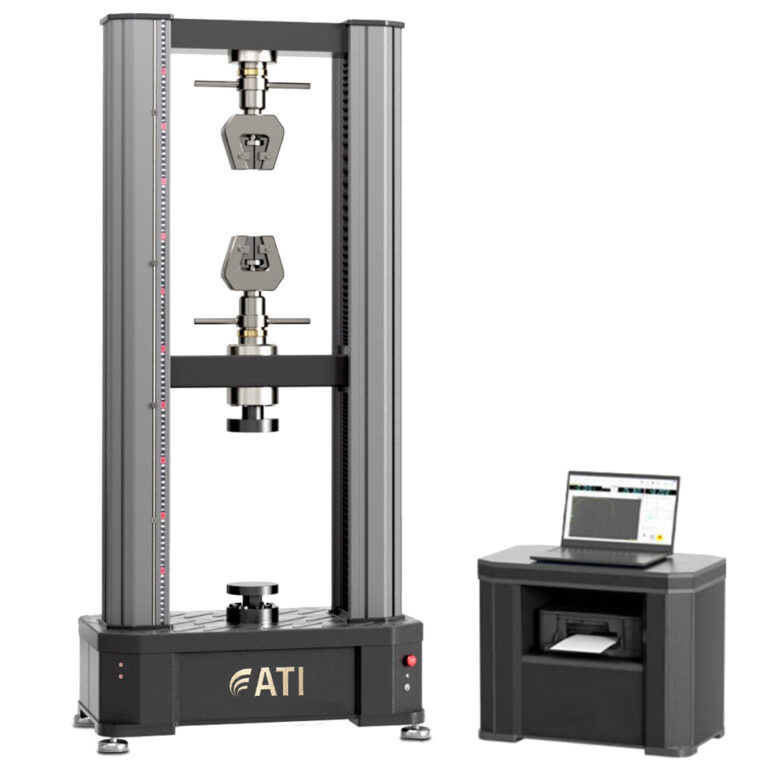
ATI UTM-Pro
The ATI UTM-Pro is equipped with pre-loaded ball screws, heavy duty bearings, and robust guidance columns, ensuring exceptional stability and performance during testing. The design features aluminum covers with chamfered corners, facilitating convenient attachment of various accessories. A high-accuracy USA load cell is incorporated, enabling precise measurement of high loads, essential for rigorous testing requirements. The machine’s remote control system allows operators to monitor key parameters, including load, displacement, and speed. It also facilitates control over critical functions such as test initiation, termination, and zero clearing, enhancing operational efficiency. To ensure safety, the ATI UTM Pro features a fully enclosed safety shield that protects users during testing. Various gripping options, including pneumatic, hydraulic, and manual wedge-type grips, can be accommodated alongside bending fix- tures, allowing for versatile testing configurations within the chamber. An integrated limit indicator further enhances safety by illumi- nating upper and lower lights when the electronic limit is touched, preventing potential sensor overloads and equipment damage. This combination of advanced features makes the ATI UTM Pro a reliable and efficient solution for material testing in diverse applications.
Load frame and Loading weight system
The frames of the ATI UTM Pro are designed with a strong emphasis on human factors to enhance safety, minimize operator fatigue, and ensure optimal flexibility during operation. Each frame integrates extremely robust crosshead guidance, delivering superior lateral stiffness and stability throughout the testing process. This design consideration significantly enhances the accuracy and reliability of results. High precision is achieved through the incorporation of preloaded precision ball screws, which facilitate rapid operation while maintaining low noise levels. This advanced mechanism not only ensures high speed performance but also guarantees exceptional position measurement accuracy, making it ideal for demanding testing applications. The load frame features a four column design supported by heavy duty pre-loaded bearings, which contribute to enhanced stiffness and structural integrity. In terms of safety, the testing machine is equipped with an automatic stop feature that activates if the change in test force exceeds a predefined threshold, thus protecting both the operator and the equipment from potential damage.
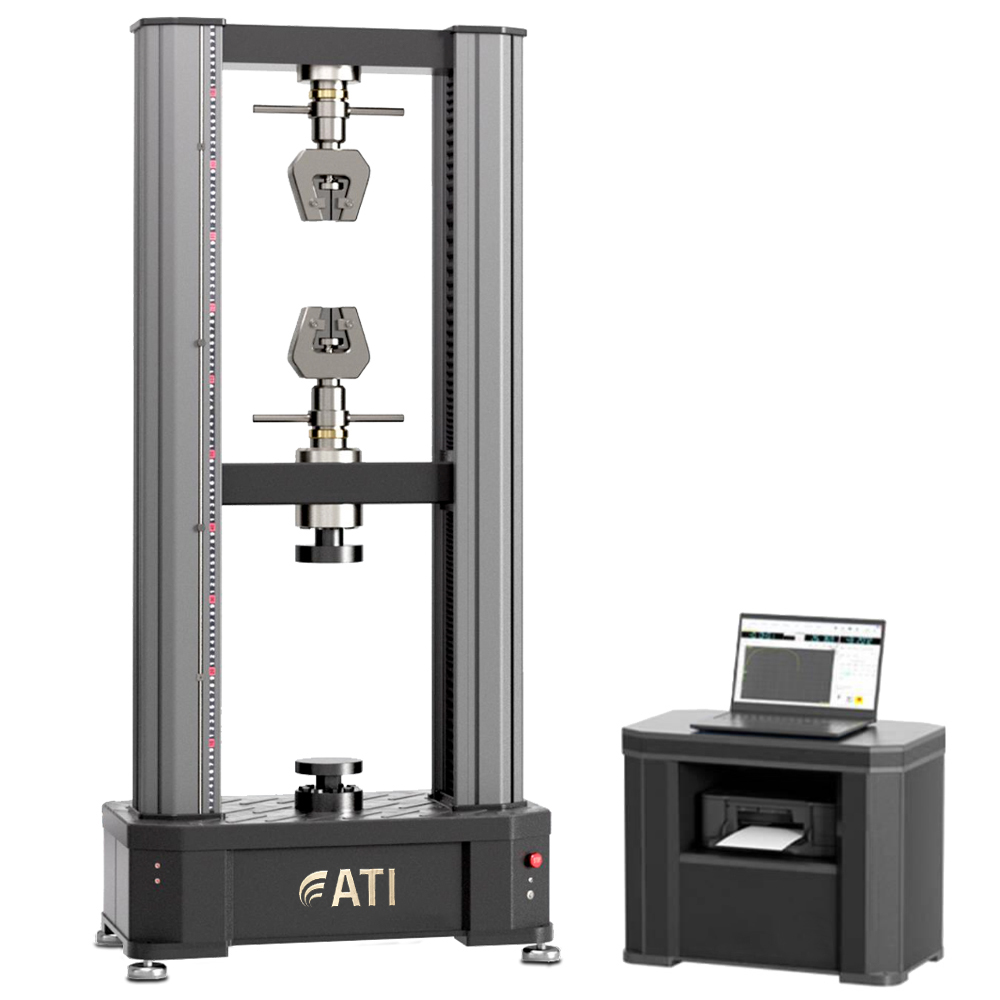
Additionally, dual over travel limits are integrated into the front console to prevent crosshead overshooting and sensor overloads. Operators can easily preset these limits to specific distances using a graduated rule along the column, ensuring precise control over testing parameters. Overall, the ATI UTM Pro combines cutting-edge engineering with user centric features to provide a comprehensive and safe testing solution. Loading weight system is the most critical aspect of mechanical testing. ATI UTM Pro is able to get the most ac- curate results. Measuring load can be from 0.4% to 100% of the rated capacity. Calibration within 0.5% accu- racy and conform to ASTM E4, ISO 7500-1, EN 10002-2, BS1610, DIN 51221 standards. This special load cell pro- vides excellent immunity to impact and size forces, rugged and low-profile measuring body with strictly symmetrical design. Mechanical protection to protect the strain area. It can be set for 105% over range protection, over load capacity of 150% without permanent zero shift and over load projection of 300% of the rated capacity withput mechanical damage.
Software
The software of the ATI UTM Pro is engineered to provide a comprehensive digital control system that enhances the precision and reliability of testing processes. Utilizing a specialized controller, the software allows for accurate digital adjustments of the zero point and gain for load, deformation, and displacement measurements. This user-friendly interface ensures ease of operation while maintaining high reliability across diverse testing environments. One of the standout features of the software is its ability to store, set, and load multiple parameters, facilitating the seamless integration of various transducers with a single load frame. This flexibility enables users to customize the testing setup according to specific requirements. Additionally, the software supports closed-loop control, allowing real-time visualization of reference curves as users adjust parameters, thus enabling immediate observation of the impact of those adjustments on test outcomes. The graphical functionality within the software is highly advanced, providing capabilities such as curve reappearance, amplification, reduction, self-adaptation, and overlaying of curves. Users can easily display and print curves within designated ranges while observing coordinates of specific test points, which aids in detailed analysis. Data processing is another critical aspect, as the software supports automatic analysis and facilitates intuitive human-machine interaction. This functionality streamlines the comparison and verification of test results, enhancing efficiency in data interpretation. Furthermore, the ATI UTM Pro software includes multilevel identity management, allowing different user roles to access specific functions. This not only accelerates operations for routine users but also bolsters system security. Test data is stored in a database as text files, making it easy for users to access and utilize various commercial report formats for further data processing. The capability to transfer data conveniently to the internet enhances collaboration and information sharing, solidifying the software’s role as a vital component of the ATI UTM Pro’s versatility and functionality.
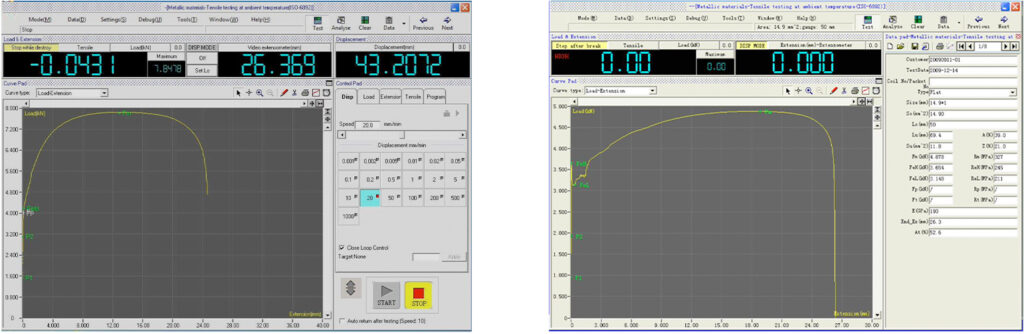
Test controller feature
The ATI UTM Pro features an advanced control system that supports three closed-loop controls: force, deformation, and displacement. Each control ring can be automatically switched, enabling seamless transitions between modes without any impact on performance. This flexibility is essential for a wide range of testing applications. The system employs up to three channels of 24-bit high-precision A/D converters, ensuring exceptional measurement accuracy. The digital output interface is capable of producing pulse signals ranging from 0 to 2 MHz, while the analog output interface provides a 16-bit precision voltage signal between -10V and +10V. These outputs are suitable for controlling servo motors, servo valves, and other actua- tors, enhancing the system’s versatility. To further improve operational efficiency, the ATI UTM Pro supports USB interface mode, significantly increasing the transmission rate and allowing for higher sampling frequencies. This capability is crucial for real-time data analysis and processing. The machine is also equipped with a sensor self-recognition system and a correction parameter memory function, enabling rapid replacement of various sensors without complex recalibration. The user interface includes an LCD display hand control box that combines aesthetic appeal with user-friendly operation. Safety features are inte- gral to the design, incorporating limit settings, overload protection, and an emergency stop function. These safety measures ensure reliable operation and protect both the equipment and the operator during testing procedures. Overall, the ATI UTM Pro delivers a sophisticated and secure testing experience, suitable for demanding applications across various industries.
Model: | ATI UTM-Pro |
Compliance Standards: | ASTM E4, ISO 7500-1, EN 10002-2, BS1610, DIN 51221 |
Testing Load Accuracy: | 100 kN |
Testing Load Range: | ± 0.5% |
Testing Load Accuracy: | 0.4% ~ 100% FS |
Load Resolution: | 1/500’000 FS |
Deformation Measuring Range: | 0.2% ~ 100% FS |
Deformation Accuracy: | ≤ + 0.5% |
Deformation Resolution: | 1/500’000 FS of the maximum deformation |
Test Control Mode: | Three Closed-Loop control, stress, strain and displacement |
Displacement Accuracy: | Within ± 0.5% of the value |
Displacement Resolution: | 0.04 μm |
Constant Force Control Range: | 0.001 ~ 5% FS/s |
Constant Force Control Range Accuracy: | When the rate is < 0.05% FS/s, it is within ± 2% of the set value. When the rate is ≥ 0.05% FS/s, it is within ± 0.5% of the set value |
Constant Deformation Force Controll Range: | 0.005 ~ 5% FS/s |
Constant Deformation Force Control Accuracy: | When the rate is < 0.05% FS/s, it is within ± 2% of the set value. When the rate is ≥ 0.05% FS/s, it is within ± 0.5% of the set value |
Crosshead Speed Range: | 0.001 ~ 500 mm/min |
Crosshead Speed Accuracy: | Within ± 0.5% of the value |