AFFRI RSD SERIE
Automatic hardness tester for rapid use
- Test loads From 3 to 187,5 kgf (From 29,42 to 1839 N) – As optional 250 kgf (2452 N)
- Rockwell and superficial Rockwell ISO 6508 / ASTM E-18 HRA – HRB – HRC – HRD – HRF – HRG – HRL – HRM – HRR / HRN – HRT
- Brinell HBWT ASTM E-103 / SO 6506 HB 30 – HB 10 – HB 5 – HB 2,5 – MPa (F/D2)
- Vickers ISO 6507 / ASTM E-92 (Indentation only) HV3 – HV10 – HV15 – HV30 – HV60 – HV100
ONE DRIVE MEASUREMENT
AFFRI Rockwell hardness testers RSD are highly accurate systems equipped with automatic preloading, loading, and measurement capabilities. The RSD AFFRI System achieves the highest level of precision in depth accuracy and measurement resolution for Rockwell tests, ensuring unmatched reliability. The advanced AFFRI System guarantees that the real indentation measurement is achieved without any interference from external factors, regardless of environmental conditions. This fully automated process streamlines testing, increasing efficiency and accuracy.
Features include:
- Auto-contact with the specimen for precise positioning
- Automatic clamping and activation of the reference surface point
- Auto preloading and loading cycles for consistent force application
- Automated measurement process for fast results
- Auto-return stroke when releasing the lever for smooth operation
Once the entire test cycle is completed, the result is immediately displayed, providing quick and reliable hardness readings for a variety of materials.
Only 3″ for one hardness test! (more with standardized dwell time)
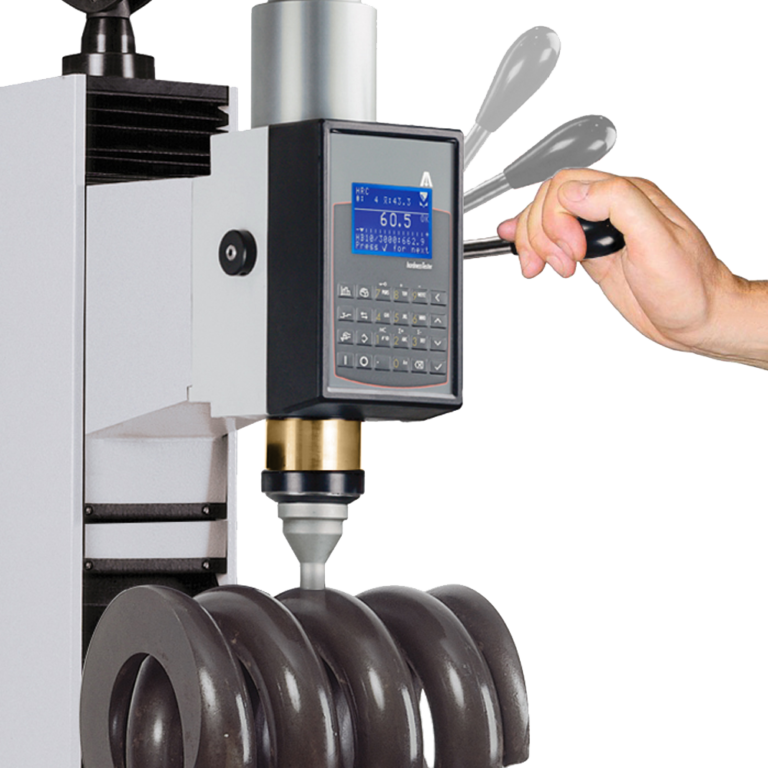
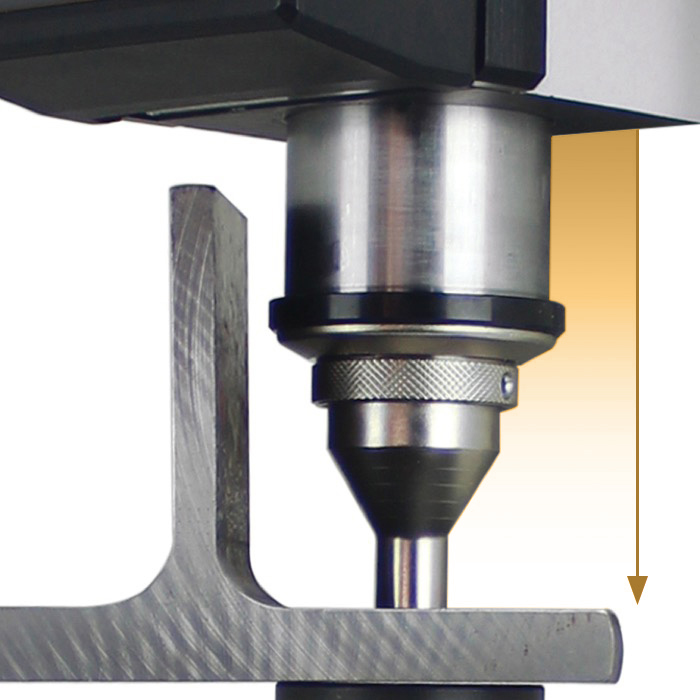
AUTOMATIC CONTACT AND TEST ACTIVATION
The Rockwell hardness testers RSD are equipped with a measuring head featuring a vertical sliding stroke of 50 mm / 2″, which includes automatic contact with the test surface for efficient testing. This stroke allows for quick and precise measurements on samples with varying thicknesses, without requiring manual adjustments to the tester head or elevating screw, improving both speed and ease of use. When testing unstable or deflecting materials, the innovative AFFRI System ensures that the tester maintains constant contact with the sample, adapting to changes in position. Thanks to its 50 mm stroke, the indenter and clamping hood follow the surface precisely, preventing loss of contact during testing. Accurate and reliable measurements are achieved on the first test, even in the most challenging conditions, minimizing the need for multiple test cycles. The repeatability and reproducibility (R&R) data provided by the system consistently rank among the best in its class, ensuring high-quality, dependable results for every test.
CLAMPING TO THE LIMIT
Secure contact with the specimen is consistently maintained throughout the entire testing process, even in the unlikely event of any movement during the operation cycle. The advanced clamping system firmly holds the specimen in place before the measurement cycle begins, and it moves in tandem with the head during the entire measuring stroke, applying constant pressure for reliable results. This ensures perfect stability for the test piece, preventing any misalignment or instability throughout the entire test cycle.
- Unwavering stability of the specimen throughout the entire testing process, ensuring precision.
- Safe and reliable testing on challenging samples, including oiled, rusty, or dirty surfaces.
- No need for external support like pedestals, simplifying the testing setup and increasing convenience.
- The indenter is carefully protected and retracted, minimizing the risk of accidental damage during tests.
- The system allows for rapid testing of long bars, tubes, or rings in just a few seconds, enhancing efficiency and productivity.
The Clamping works automatically when pulling the lever
It can’t be easier than this
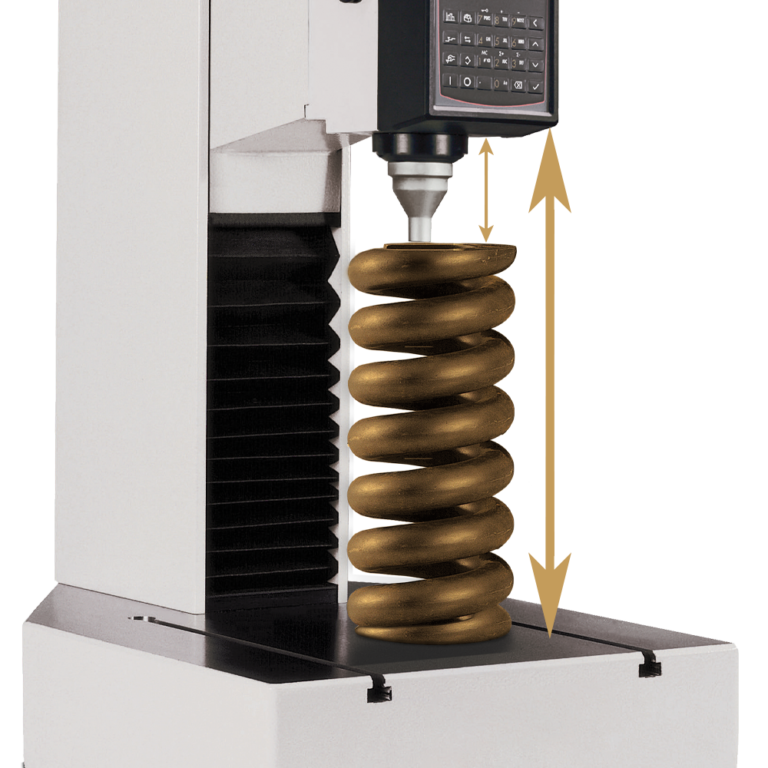
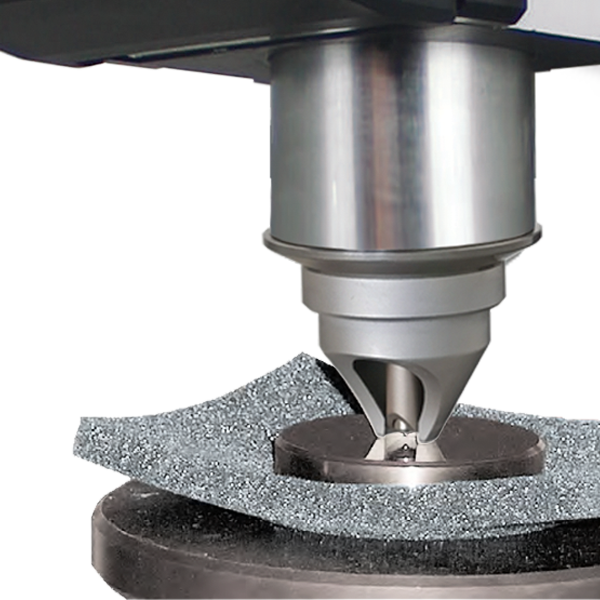
THE INCREDIBLE AFFRI PERFORMANCE
We subject each instrument to rigorous testing under extreme conditions to ensure the precision and reliability of every measurement. The top surface referencing design effectively reduces errors typically associated with anvil misalignment or contamination (such as dust or rust). This design reduces sample preparation time while simultaneously improving both accuracy and testing speed, optimizing the entire testing process. Absolute accuracy is guaranteed from the first indentation, as the constant and stable clamping surface ensures reliable measurement without the need for retesting. The first result obtained is definitive and ABSOLUTE, ensuring exceptional consistency and precision in all tests. This design principle ensures the highest level of reliability across a wide range of applications.
EXTRA FEATURES
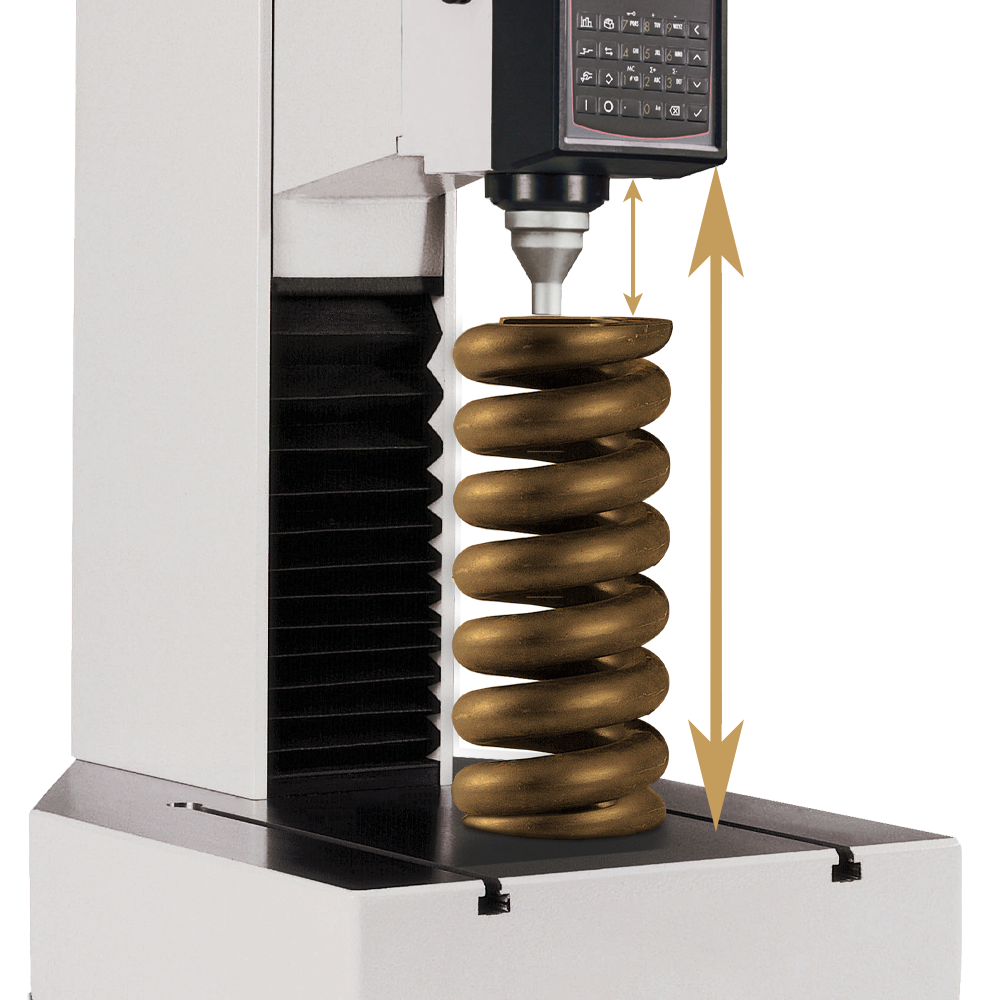
INFINITE CAPACITY
With a vertical stroke of 700 mm or greater, the adjustable tester head allows for effortless measurements on large components, reaching areas at the top of the sample that would be challenging to measure with standard testers.
EXTRA FEATURES
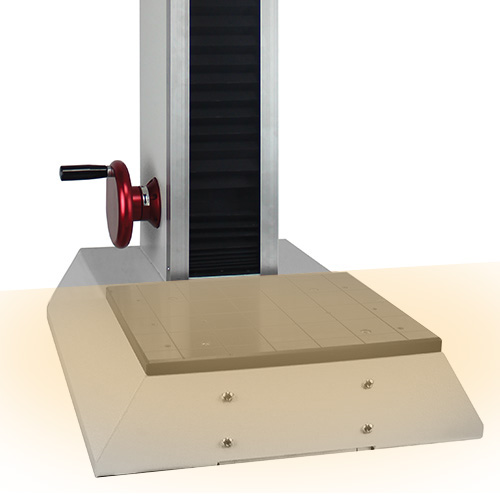
OPEN SPACE
The expansive work surface can support weights exceeding 2000 kg, ensuring stable hardness measurements on large or irregularly shaped components. It also provides a convenient and reliable base for testing smaller pieces.
EXTRA FEATURES
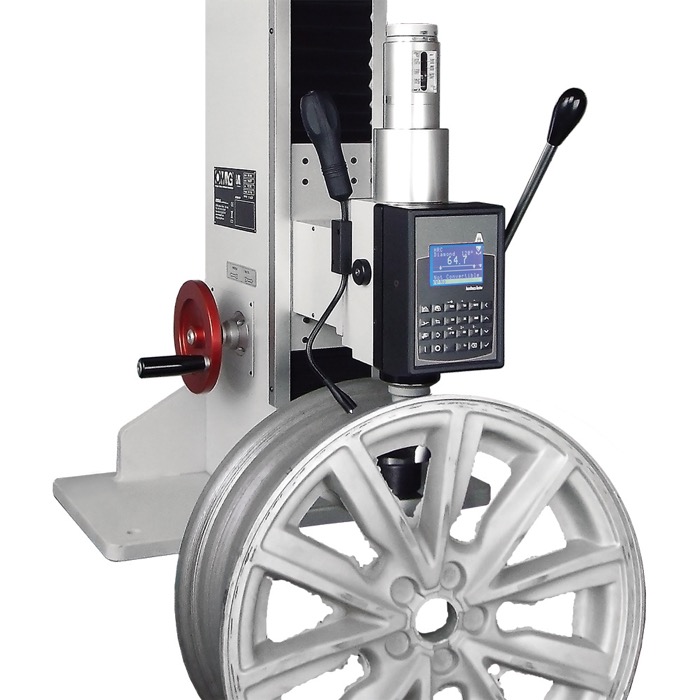
CUSTOM BASES
An optional, interchangeable base is available for hardness testing on externally ring-shaped tubes, cylindrical surfaces, and samples of varying diameters. Manufactured by AFFRI, the tester stand can be customized to meet any specific requirements.
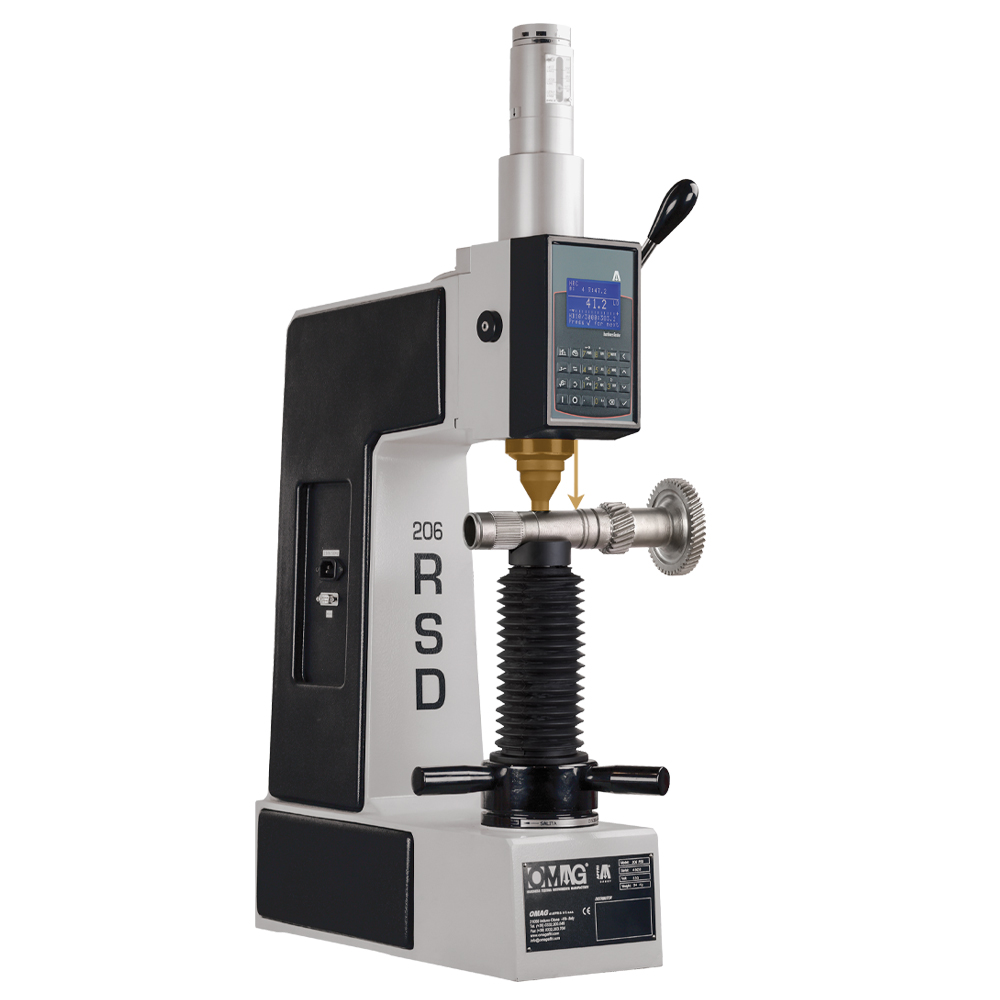
AFFRI RSD SERIE
Automatic hardness tester for rapid use
- Test loads From 3 to 187,5 kgf (From 29,42 to 1839 N) – As optional 250 kgf (2452 N)
- Rockwell and superficial Rockwell ISO 6508 / ASTM E-18 HRA – HRB – HRC – HRD – HRF – HRG – HRL – HRM – HRR / HRN – HRT
- Brinell HBWT ASTM E-103 / SO 6506 HB 30 – HB 10 – HB 5 – HB 2,5 – MPa (F/D2)
- Vickers ISO 6507 / ASTM E-92 (Indentation only) HV3 – HV10 – HV15 – HV30 – HV60 – HV100
ONE DRIVE MEASUREMENT
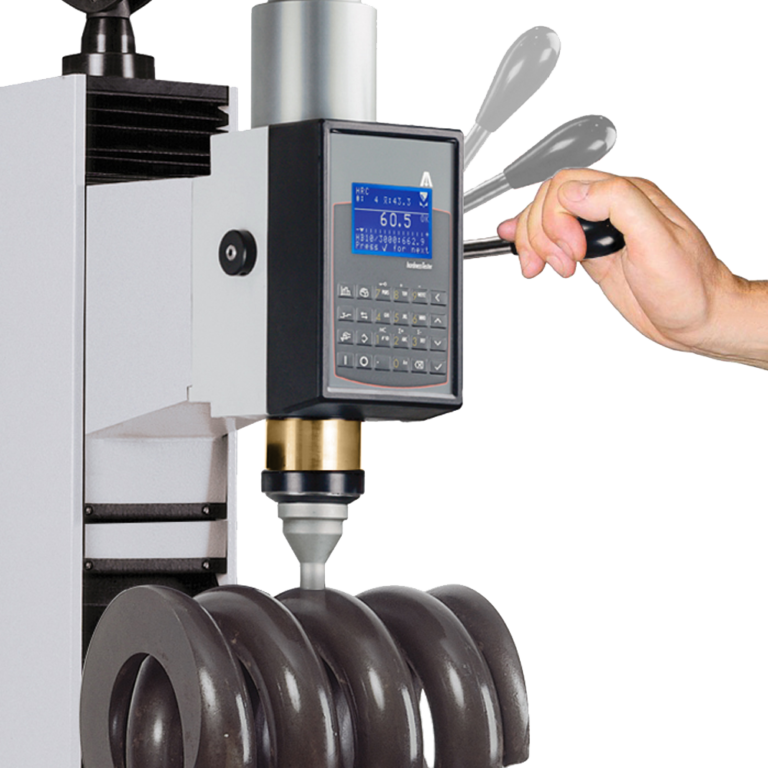
Features include:
- Auto-contact with the specimen for precise positioning
- Automatic clamping and activation of the reference surface point
- Auto preloading and loading cycles for consistent force application
- Automated measurement process for fast results
- Auto-return stroke when releasing the lever for smooth operation
Once the entire test cycle is completed, the result is immediately displayed, providing quick and reliable hardness readings for a variety of materials.
Only 3″ for one hardness test! (more with standardized dwell time)
AUTOMATIC CONTACT AND TEST ACTIVATION
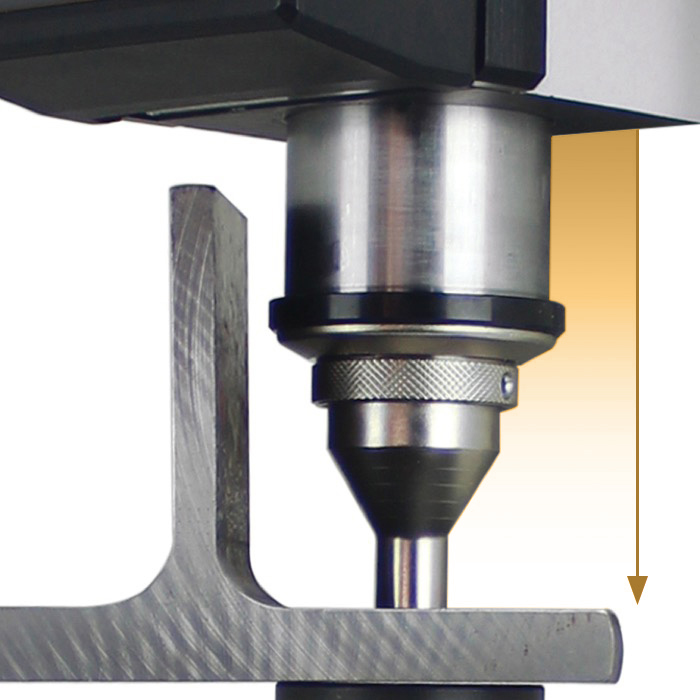
CLAMPING TO THE LIMIT
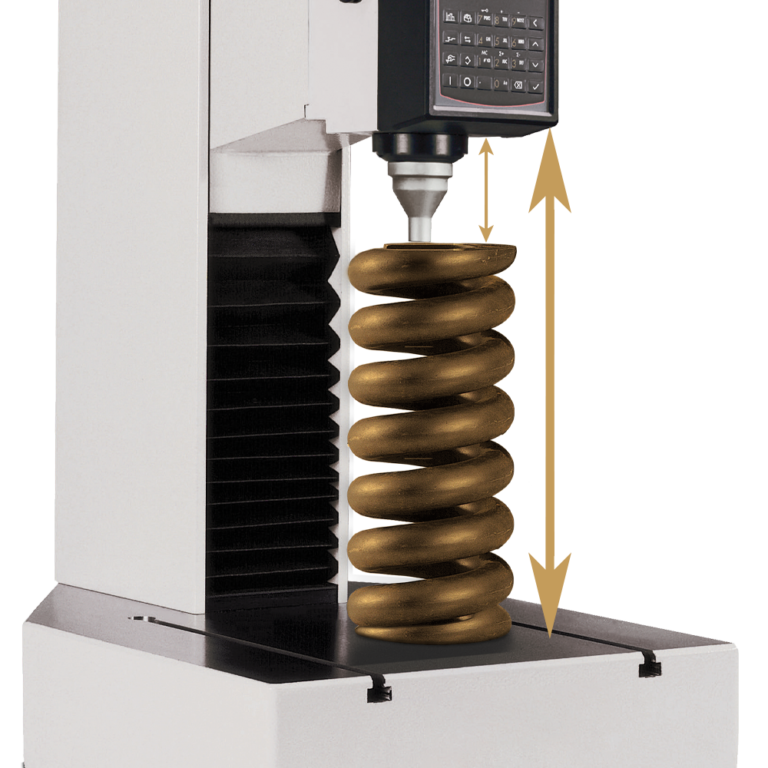
- Unwavering stability of the specimen throughout the entire testing process, ensuring precision.
- Safe and reliable testing on challenging samples, including oiled, rusty, or dirty surfaces.
- No need for external support like pedestals, simplifying the testing setup and increasing convenience.
- The indenter is carefully protected and retracted, minimizing the risk of accidental damage during tests.
- The system allows for rapid testing of long bars, tubes, or rings in just a few seconds, enhancing efficiency and productivity.
The Clamping works automatically when pulling the lever
It can’t be easier than this
THE INCREDIBLE AFFRI PERFORMANCE
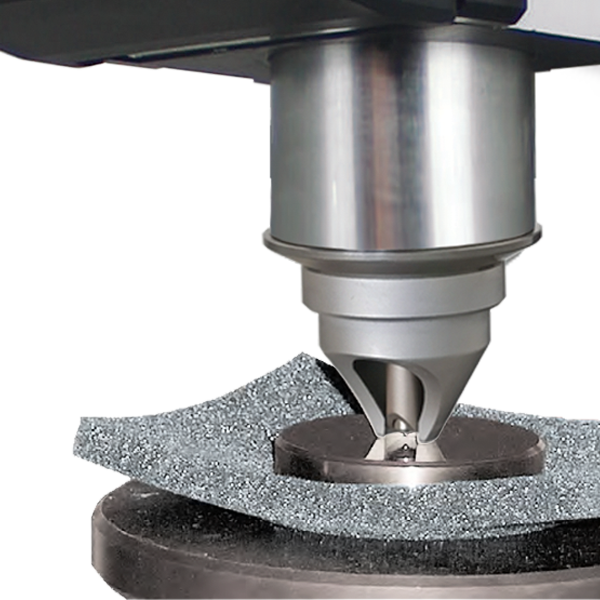
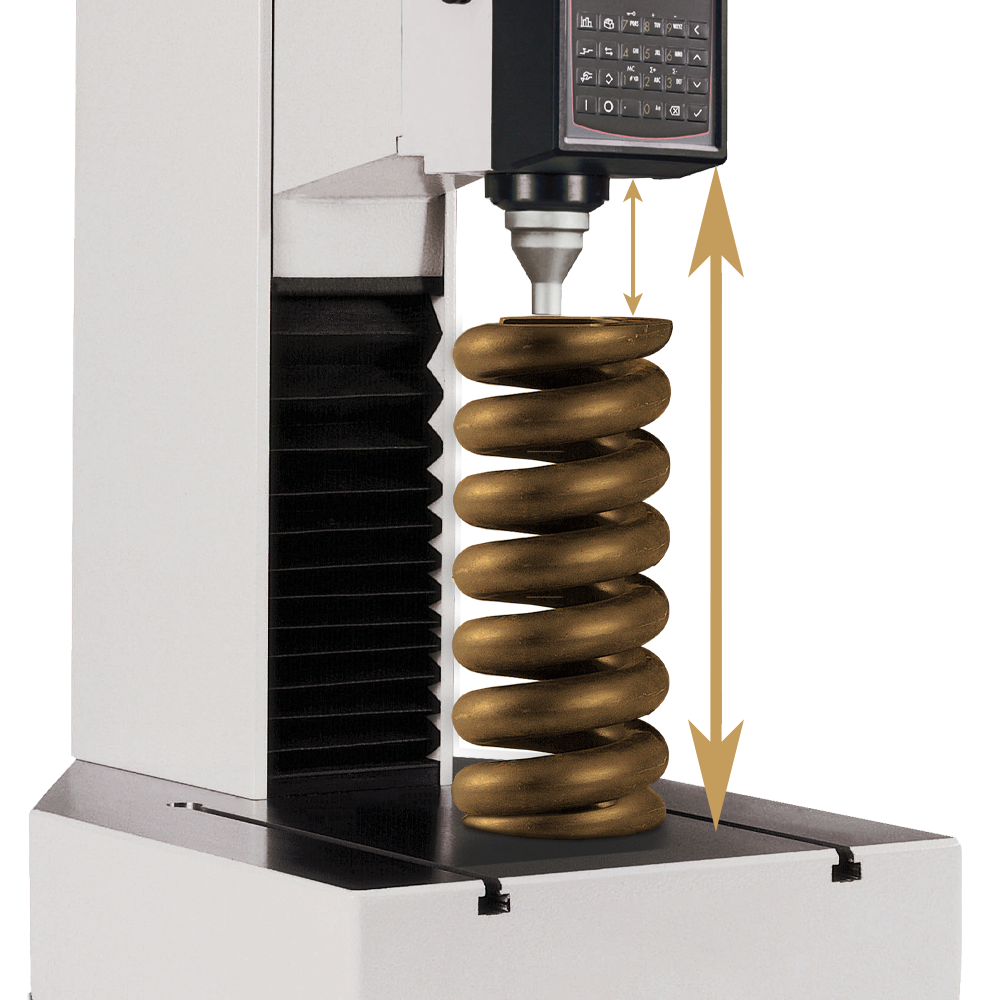
INFINITE CAPACITY
With a vertical stroke of 700 mm or greater, the adjustable tester head allows for effortless measurements on large components, reaching areas at the top of the sample that would be challenging to measure with standard testers.
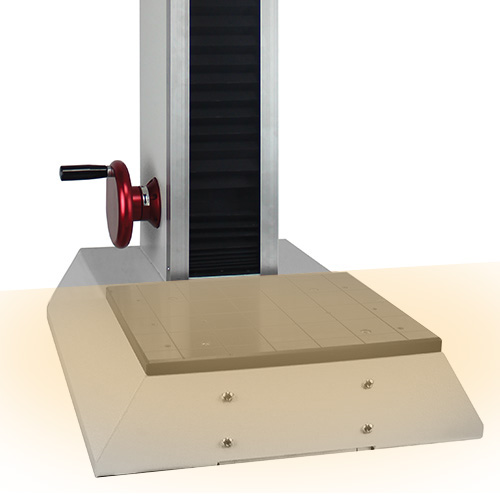
OPEN SPACE
The expansive work surface can support weights exceeding 2000 kg, ensuring stable hardness measurements on large or irregularly shaped components. It also provides a convenient and reliable base for testing smaller pieces.
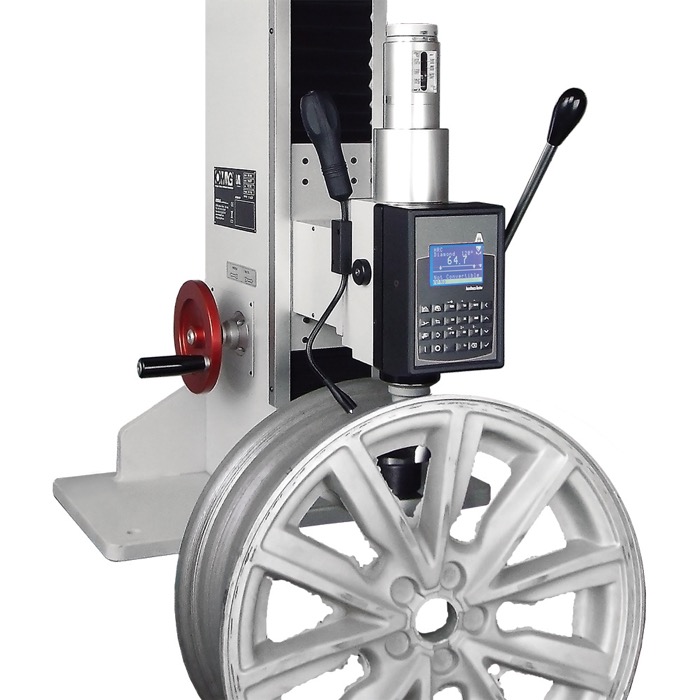
CUSTOM BASES
An optional, interchangeable base is available for hardness testing on externally ring-shaped tubes, cylindrical surfaces, and samples of varying diameters. Manufactured by AFFRI, the tester stand can be customized to meet any specific requirements.